Foreword to Investment Casting Process
The Investment Casting Process is something that has fascinated me for years. At first glance, it might seem like a complicated craft, but once you dive into it, the intricate beauty of the method becomes clear. It’s the kind of process that feels like you’re shaping the future from something so delicate as wax.
I remember the first time I encountered the Precision casting technique. The sheer precision involved left me in awe. Picture this: creating a pattern out of wax, knowing that each subtle detail will be immortalized in metal. It’s a delicate balance of art and engineering.
The process starts with a wax model, which serves as the blueprint. It’s dipped in ceramic slurry, like wrapping a fragile gift, one layer at a time, until it’s ready to withstand the molten metal. Each step requires patience and a steady hand, but it’s worth it when you see the final result.
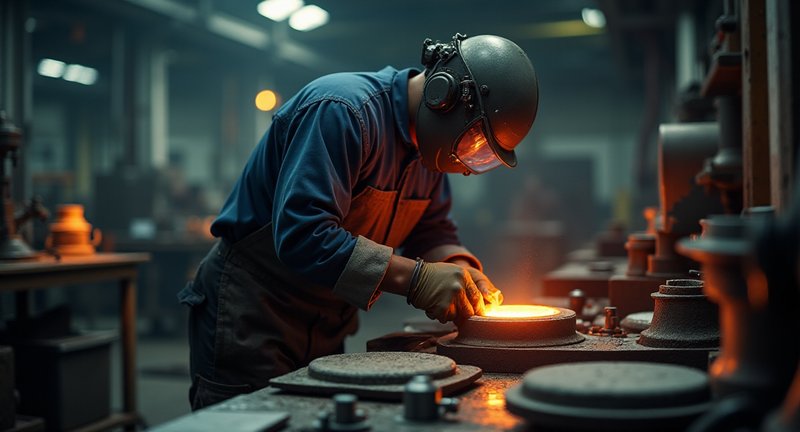
What’s remarkable about the Wax-molded metal casting is its versatility. Whether it’s for small, intricate parts or large, complex designs, this method holds the capability to bring a vision to life with precision. And trust me, seeing that metal piece emerge after the mold is shattered it’s a kind of magic that never gets old.
If you’re wondering whether it’s worth diving into, I say yes. The Lost-wax fabrication method has not only stood the test of time but has evolved into a cornerstone of modern manufacturing. It’s a blend of ancient technique and modern innovation, an ongoing dance between creativity and precision.
The Role of Investment Casting Process in Manufacturing
In relation to precision in manufacturing, few techniques hold as much significance. I’ve worked with many methods, but there’s one that consistently delivers near-perfect detail with remarkable efficiency. Imagine a process that allows you to craft complex geometries with minimal waste, where accuracy isn’t a bonus – it’s the baseline.
What always surprises me is how this method achieves such intricate detail. Molten metal flows into a meticulously crafted mold, creating parts that look as if they were sculpted by hand. The beauty lies in how it’s both delicate and robust, able to produce components that are essential for high-performance industries.
What makes it even more fascinating is its versatility. Whether I’m dealing with aerospace components or fine art sculptures, this approach adapts seamlessly. The raw materials, the patterns – they all seem to come together like a carefully planned symphony, hitting every note with precision.
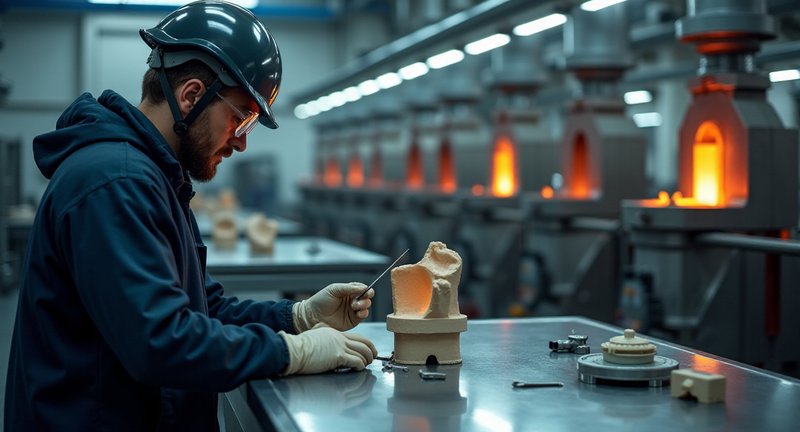
But it’s not just the precision that makes this process stand out. It’s also incredibly cost-effective. By reducing material waste and streamlining production, it offers financial advantages that can’t be ignored. When I’ve worked on projects with tight budgets, this has been a game-changer.
What I love most is how it blends old-world craftsmanship with modern technology. In a world that often feels rushed, it’s refreshing to see a method that values quality and detail as much as speed. This combination is why it remains a staple in my toolbox.
What is Precision Casting?
Precision casting is the art of shaping metal with extreme accuracy, and it’s a method that has fascinated me for years. Imagine being able to create complex shapes that require very little to no machining afterward – this is the magic of precision casting. It’s like sculpting but with molten metal, and it involves a level of attention to detail that sets it apart from other metalworking techniques.
When I first dove into this world, what stood out to me was how precision casting combines ancient techniques with modern technology. You’re working with molten alloys, creating intricate forms that might otherwise be impossible with traditional methods. This approach allows manufacturers to produce parts with tight tolerances and complex geometries – think about the gears in an aircraft engine or medical instruments that require absolute precision.
Here’s a breakdown of why precision casting is so valuable:
- Versatility: Whether you’re dealing with stainless steel, aluminum, or exotic metals like titanium, precision casting can handle it.
- Minimal waste: It’s an eco-friendly choice. Since parts are created near their final shape, there’s less need for post-production work, which means fewer wasted materials.
- Complexity: You can cast detailed and intricate parts in one go, avoiding the need for assembly or welding.
- High-quality surface finish: The process results in smooth finishes, reducing the need for further polishing or treatments.
One of the other great things about precision casting is the ability to scale production. Whether you’re making a one-off prototype or mass-producing components, the method remains efficient.
If you’re working in an industry where precision is non-negotiable, from aerospace to healthcare, this is the route to take. It’s a blend of craftsmanship and science, resulting in perfect parts every time.
The History and Evolution of Metal Casting
When diving into the history and evolution of metal casting, we uncover a fascinating tale that spans millennia. Picture ancient artisans, hunched over their primitive forges, shaping metal with rudimentary tools. Their techniques laid the groundwork for what we now consider advanced casting methods.
Initially, casting was a straightforward affair. The process began with melting metal, pouring it into a mold, and letting it solidify. This approach, simple as it sounds, was revolutionary in its time. As centuries passed, metal casting evolved significantly.
Key milestones in this evolution include:
- Ancient Beginnings: The earliest evidence of metal casting dates back to the Bronze Age. Artisans used sand and clay molds to create weapons, tools, and ornaments.
- Medieval Innovations: During the Middle Ages, techniques became more sophisticated. The use of investment materials (not to be confused with our modern-day processes) allowed for finer details and more complex shapes.
- Industrial Revolution: This era brought about the mechanization of casting. The introduction of steam power and automation revolutionized production, making it faster and more efficient.
- Modern Techniques: Today, metal casting encompasses a range of high-tech methods, from precision casting to advanced alloys. These innovations cater to industries requiring exceptional accuracy and durability.
In my journey through the world of metal casting, I’ve witnessed firsthand how each era has contributed to the richness of this craft. From the rudimentary practices of early civilizations to the precision of today’s technologies, metal casting is a testament to human ingenuity and progress.
As we continue to innovate, it’s clear that the history of metal casting is not just about technique but also about the people who have shaped it. Their creativity and persistence drive the evolution of this essential craft.
Key Steps in the Wax Casting Method
Let’s talk about one of the most intriguing and precise techniques in metal casting: the wax casting method. Now, if you’re new to this, don’t worry. I’ve been there, and I’m going to walk you through it like an old friend. Here’s a breakdown of the key steps that have been honed over centuries.
First, create your wax pattern. This is like sculpting a miniature version of what you want the final metal piece to look like. The wax is shaped meticulously, and trust me, the more detailed, the better. You’ll get to appreciate this fine art as every curve and contour is perfectly replicated in the final product.
Next, assemble the wax patterns. If you’re working with multiple pieces, you’ll need to join them onto a wax “tree.” It’s exactly what it sounds like – a structure that allows molten metal to flow smoothly during the final phase. This step reminds me of connecting puzzle pieces, each fitting into a larger, cohesive design.
Then, you’ll dip the wax tree in ceramic slurry, coating it layer by layer. The goal here is to build up a strong ceramic shell around the wax. Imagine giving your wax model a protective suit of armor – because it’s going to get a little fiery soon.
Now, the part that gets me every time – melting out the wax. Once the ceramic shell is dry, it’s placed in a kiln where the wax melts and leaves behind a perfect cavity. This is where the magic happens, folks.
As a matter of fact, pour molten metal into the mold. After cooling, break away the ceramic, and you’ll have your final, solid metal piece. This is where all the hard work comes to life, quite literally in solid form.
The Role of Wax Patterns in Casting
When I think about casting, my mind often wanders to the delicate art of wax patterns. It’s a silent hero in shaping precision. Wax, in its moldable state, allows for an intricate dance between creativity and engineering.
In my experience, wax patterns are like blueprints you can touch. They define not only the final form of the metal but also its hidden intricacies, which only reveal themselves when the metal cools. What fascinates me is how wax, such a fragile material, holds the responsibility of shaping something as unyielding as metal.
Picture this: you sculpt an intricate wax figure, and soon it becomes the heart of something far stronger. Every curve, every edge matters because it’s what the final casting will mirror. And that’s where the true beauty lies.
The wax pattern isn’t just a fleeting phase. It’s a crucial stage where flaws can be caught early. Believe me, missing an imperfection here could ruin hours of labor down the line. It’s a testament to the importance of doing it right the first time.
Once the wax has done its job, it’s as if it steps aside gracefully, allowing the next stage to take the spotlight. But its impact? That stays, locked forever in the metal that follows.
How to Create Molds for Investment Casting
When diving into the world of creating molds for investment casting, it feels like stepping into a high-stakes art project where precision meets craftsmanship. From my experience, the Investment Casting Process is akin to sculpting your ideas into reality with meticulous care.
First things first, the mold design is crucial. Imagine it as the blueprint of your final product, defining every intricate detail. The process begins with a detailed pattern, often crafted from wax or a similar material, which will be transformed into the final mold.
Once the pattern is ready, it’s time for the magic of coating. You’ll encase the pattern in a ceramic shell that hardens to create a cavity for molten metal. This stage is where the Precision metal casting technique truly showcases its finesse, requiring an exact blend of materials and temperatures.
After the shell has solidified, it’s heated to remove the pattern, leaving a hollow mold ready for casting. Pouring molten metal into this cavity is like filling a cookie cutter with dough, but with far more precision. The metal cools, solidifies, and voila your mold has done its job.
As a matter of fact, you’ll break away the ceramic shell to reveal the casted piece. The lost wax casting method allows for incredible detail and complexity, making it an ideal choice for creating high-quality, intricate components. Trust me, seeing the final product emerge from the mold is nothing short of rewarding.
The Importance of Ceramic Shells in Metal Casting
In my journey through the world of metal casting, I’ve come to appreciate the unsung hero: ceramic shells. These intricate structures play a pivotal role in delivering precision and quality that you simply can’t overlook.
Imagine a delicate yet robust cocoon enveloping molten metal. That’s precisely what a ceramic shell does, providing the perfect mold for complex shapes that challenge traditional methods.
When I first encountered ceramic shells, I was struck by their ability to withstand extreme temperatures. This resilience allows for the creation of parts that require not just strength, but an artistry that leaves a lasting impression.
What’s more, the surface finish produced by these shells is often exquisite. The fine details captured are a testament to the shell’s capability, resulting in components that can often be used straight from the mold without further refinement.
For anyone venturing into metal casting, understanding the significance of ceramic shells can transform your approach. They enable not just efficiency but also creativity in design, allowing you to push boundaries in your projects.
So, next time you think about metal casting, remember this: the ceramic shell is not just a support structure; it’s a key player in the symphony of precision engineering. It’s fascinating how such a seemingly simple element can elevate the entire process, don’t you think?
Understanding the Burnout Process in Casting
Burnout in casting isn’t just some technical step it’s the moment where everything comes together or falls apart. I’ve seen firsthand how this phase can make or break your entire production run. It’s that critical time when your mold, after all the painstaking work, gets heated and any wax or impurities evaporate, leaving only the shell behind. Sounds straightforward, but it can be where tension peaks.
Imagine watching the shell, knowing that any flaw in this stage means rework, delays, and headaches. That delicate balance of temperature and timing becomes more than just numbers on a gauge it’s the difference between smooth sailing and chaos. It’s in these moments where the real skill of casting professionals shines, a kind of hidden artistry.
When the burnout process is flawless, you breathe a sigh of relief. You’re halfway home. But when something goes awry, and I’ve been there more times than I care to count, it feels like watching sand slip through your fingers. Fixing errors at this stage? Not easy. It’s almost like running a marathon and tripping just steps from the finish line.
The heat, the precision, and the waiting it all becomes part of a dance you hope ends perfectly. But every so often, a tiny miscalculation can leave you scrambling. If you’ve been in the game long enough, you know to anticipate the unexpected, but no one likes to gamble when it comes to final outcomes.
The Role of Heat Treatment in Precision Casting
In the nature of precision casting, the heat treatment process is akin to the secret sauce that elevates a dish from ordinary to extraordinary. My experience with heat treatment has shown me how crucial it is for achieving the ultimate material properties in castings, especially when precision is the name of the game. Let’s ascertain the fascinating role it plays.
Why Heat Treatment Matters
Heat treatment is not just about raising temperatures; it’s about transforming materials at a molecular level. Here are some ways it contributes to precision casting:
- Enhances Strength and Durability: By adjusting the heat and cooling rates, we can significantly enhance the tensile strength of the final product, ensuring it withstands harsh environments.
- Improves Ductility: This process also helps in making materials more ductile, allowing for better flexibility and formability, which is essential for intricate designs.
- Reduces Residual Stresses: A well-executed heat treatment can alleviate internal stresses that develop during the casting process, minimizing the risk of deformation or failure.
My Personal Takeaway
From my own experience, I’ve seen how meticulous attention to heat treatment can yield impressive results. Whether you’re working on aerospace components or intricate art pieces, understanding the thermal profiles is key.
So next time you think of casting, remember that heat treatment isn’t just a step in the process; it’s a transformative art form that can redefine the capabilities of your materials.
Material Options for the Casting Process
When dealing with choosing materials for casting, it’s like standing at a buffet with endless options, but instead of food, you’re choosing metals, alloys, and ceramics. Each material has its own quirks, advantages, and maybe a couple of quirks you didn’t expect. Let me walk you through some of my top picks from personal experience.
First off, steel is your reliable, heavy-duty option. It’s strong, durable, and, frankly, used in everything from automotive parts to construction equipment. But be prepared working with steel can be like molding a block of ice in your hands: it needs precision and heat.
Aluminum, on the other hand, is the lighter cousin of steel. It’s like that flexible friend who goes along with whatever plans you make. Aluminum is perfect for projects that require lightness without sacrificing strength think aerospace components or bike frames.
Then there’s bronze, a bit of an underdog in the casting world. It’s rich in history (think ancient sculptures), and its wear resistance makes it ideal for bearings, gears, and art pieces alike. Plus, it has this warm, almost golden hue that gives any project a classy touch.
Now, if you want something more sophisticated, ceramics could be your wildcard. They can handle extreme temperatures and have excellent resistance to wear. However, they’re like that friend who’s a little high-maintenance: you have to treat them just right, or they’ll crack under pressure.
A few more materials to consider:
- Copper: Excellent for electrical components, but prone to corrosion.
- Titanium: Ultra-strong but expensive, a true power player.
- Nickel alloys: Heat resistant, often used in jet engines and turbines.
So, what’s your choice? It all boils down to your project’s needs. Trust me, picking the right material can be the difference between a product that lasts a lifetime and one that barely makes it off the assembly line.
Types of Alloys Used in Precision Casting
When discussing precision casting, the choice of alloy can be a game changer. I’ve had the chance to work with a variety of materials, and each one brings its own character to the table, much like different players on a sports team.
Aluminum alloys, for instance, are light as a feather yet incredibly strong. They’re often my go-to for projects requiring a delicate balance between weight and durability. There’s something satisfying about how these alloys flow into intricate molds, capturing every detail with precision.
Then there’s stainless steel oh, the beauty of its resistance to corrosion! It shines like a knight’s armor, ready to face the elements. I often find myself gravitating towards this alloy for applications where longevity is crucial, and trust me, it pays off in spades.
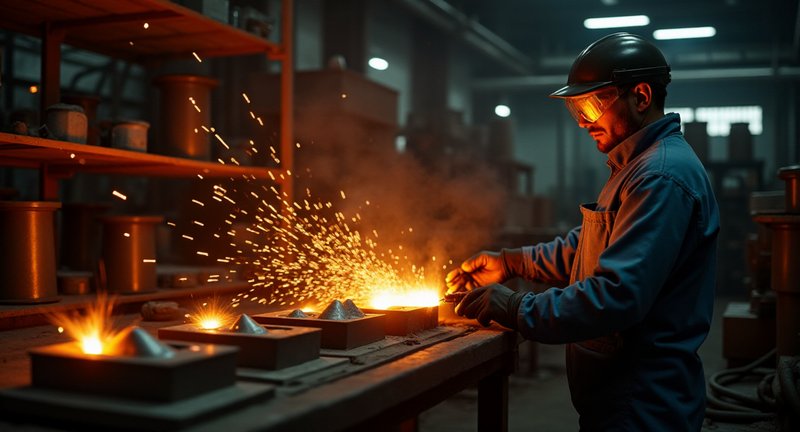
Bronze, with its warm, golden hue, adds a touch of elegance to any project. This alloy is perfect when a touch of artistry is required. I’ve seen sculptures and fixtures made from bronze stand the test of time, retaining their charm through the years.
As a matter of fact, we can’t overlook the versatility of titanium. Its lightweight nature combined with extraordinary strength makes it a favorite in industries like aerospace. It feels almost futuristic, doesn’t it? I can’t help but marvel at how this alloy pushes the boundaries of what’s possible in casting.
In my experience, understanding the nuances of these alloys is essential. Each has its own story to tell, and when you listen closely, the results can be breathtaking.
Investment Casting Process: An In-Depth Examination
Let’s dive deep into a method that has been around for centuries, yet still holds its place in modern manufacturing. This approach isn’t just about shaping metal; it’s about precision, detail, and efficiency. If you’ve ever marveled at the intricacy of a metal part, chances are, it was created using this technique.
The journey starts with creating a wax model. Yes, wax. The first time I saw this, I thought I had wandered into a candle-making workshop. But the wax model is key because it’s an exact replica of what the final product will look like. After that, things get serious. The wax is dipped repeatedly in a ceramic slurry to form a hard shell. It’s a bit like layering on coats of paint, but here, each coat adds strength.
Next, the wax is melted out, leaving behind an empty shell. Now, here’s the exciting part: molten metal gets poured into this hollow form, filling every nook and cranny of that precise mold. Once cooled and hardened, the shell is broken away to reveal the metal piece inside, ready for any final touches.
Here’s why this method shines:
- Detail perfection: It can handle complex, intricate designs with ease.
- Material variety: Works with an impressive range of metals, from stainless steel to titanium.
- Consistency: Produces near-identical parts every time, which is critical in industries like aerospace.
- Efficiency: Reduces material waste, and who doesn’t like being both effective and sustainable?
So, whether you’re creating a turbine blade or a jewelry clasp, this process is a brilliant blend of ancient artistry and cutting-edge technology.
Benefits of Using Lost Wax Casting
When I first grasped the world of lost wax casting, I was captivated by its transformative potential. This ancient technique, often shrouded in mystery, has numerous benefits that can enhance both artistry and functionality. Let me share some insights from my journey.
1. Precision and Detail
Lost wax casting allows for intricate designs and fine details that are nearly impossible to achieve through other methods. The fluidity of molten metal fills every crevice of the mold, capturing even the most delicate features.
2. Versatility of Materials
One of the ultimate joys of this technique is the ability to use a wide range of metals. Whether you’re working with silver, gold, or even more exotic alloys, the casting process accommodates them all, opening doors to creative possibilities.
3. Reduced Waste
Embracing this method often leads to less material waste. The wax model is entirely consumed in the process, ensuring that what remains is only the desired final product. This not only saves resources but also adds an eco-friendly touch to your crafting.
4. Cost-Effectiveness
While there may be initial costs associated with equipment, lost wax casting can be remarkably economical in the long run. The ability to produce small batches efficiently means lower overheads and the potential for greater profit margins.
5. Unique Artistry
The freedom to create custom designs means that your work can stand out in a crowded market. Each piece produced through this method is unique, often embodying a story that resonates with potential buyers.
So, whether you’re a seasoned craftsman or a curious beginner, I encourage you to explore the enchanting benefits of lost wax casting. It’s a journey well worth taking!
Industrial Applications of the Wax Casting Method
In the context of the industrial applications of the wax casting method, the possibilities are as vast as they are fascinating. From my experience, this technique has carved out a significant niche in various sectors due to its precision and versatility. Let’s pinpoint some of the standout applications:
-
Aerospace Components: In an industry where every gram counts, wax casting allows for the production of lightweight yet robust parts. The intricate designs achievable through this method ensure optimal performance in demanding environments.
-
Medical Devices: Picture this: highly complex surgical instruments crafted with unparalleled accuracy. The wax casting method shines here, creating tools that can be tailored for specific procedures, ultimately enhancing patient care.
-
Automotive Engineering: Here, the allure lies in both form and function. Parts such as engine components and turbochargers benefit from the high strength-to-weight ratio, crucial for modern vehicles aimed at fuel efficiency.
-
Artistic Creations: Beyond utility, the artistic realm also embraces this method. Sculptors and artisans utilize wax casting to transform their creative visions into tangible masterpieces, reflecting a unique blend of technology and artistry.
-
Jewelry Making: I can’t help but admire how this technique revolutionizes the jewelry industry. Intricate designs that would be nearly impossible to achieve through traditional methods are now a reality, allowing for stunning pieces that captivate the eye.
In my journey through various industries, I’ve seen firsthand how this method not only meets but exceeds the demands of modern manufacturing. It’s a fascinating intersection of art and engineering, driving innovation forward.
Need More Info?
Why is it called precision wax casting?
The term ‘investment casting’ comes from the process of surrounding, or ‘investing,’ a wax pattern with a ceramic slurry. The slurry hardens to form a mold, and once the wax is melted and drained away, molten metal is poured into the cavity left behind. This method has been historically referred to as ‘investment’ due to the layering of the ceramic around the wax, investing it in multiple coats until a solid mold is created.
What is the sequence of investment casting?
The sequence of the lost wax casting method begins with the creation of a wax pattern, which is a replica of the desired part. This wax pattern is assembled onto a wax tree, then repeatedly coated in ceramic slurry and sand to build up a hard shell. After the shell is cured, the wax is melted out, leaving a hollow mold. Molten metal is poured into the mold, and after cooling, the ceramic shell is broken away, revealing the final metal casting.
How long is the ceramic mold casting?
The length of the fine-detail metal casting varies depending on the complexity and size of the part being cast. Generally, the process can take several days to a few weeks. The creation and drying of the ceramic mold require careful timing to ensure it is strong enough to withstand molten metal. The drying process alone can take multiple days, while the actual casting and finishing steps are faster, ranging from hours to days depending on the post-processing needed.
What is the difference between investment casting and casting?
Investment casting is a specific form of casting that uses a wax pattern and ceramic shell mold, offering high precision and detail. In contrast, general casting refers to any method of pouring liquid material, such as metal, into a mold to form a shape. Investment casting allows for finer, more intricate details than other casting methods, like sand casting, which may have limitations in surface finish and complexity.
What is the meaning of complex-shape casting process?
The precision wax casting involves creating a detailed, expendable wax model, which is surrounded by a ceramic material to create a mold. Once the mold is formed and the wax is removed, molten metal is poured into the hollow mold to form the final product. This process is known for producing parts with excellent dimensional accuracy, fine surface finish, and the ability to cast complex shapes with minimal machining.
What is the history of investment casting?
Investment casting has ancient origins, dating back over 5,000 years to early civilizations like Mesopotamia and Egypt, where it was used to produce jewelry, idols, and small sculptures. The process evolved over centuries, but its modern resurgence began in the 19th century with advancements in industrial applications, particularly during World War II when it was utilized to manufacture precision parts for aircraft engines. Today, it is widely used across various industries, including aerospace, automotive, and art.
Why choose investment casting?
Investment casting is chosen for its ability to produce highly accurate and complex parts with a superior surface finish. It reduces or eliminates the need for extensive machining, which can save time and costs. The process is also versatile, allowing for the casting of a wide range of metals, including stainless steel, bronze, and aluminum. Additionally, it supports the production of both small and large quantities, making it a flexible choice for various industries.
How is investment casting different than shell casting?
Investment casting and shell casting both use ceramic molds, but investment casting typically involves the use of a wax pattern, while shell casting may use sand or other materials to form the mold. Shell casting often refers to the shell mold casting process where a thin shell is formed around a pattern, but it usually involves a different molding process than investment casting. Investment casting is more precise and used for smaller, intricate parts, whereas shell casting is often employed for larger components.
What are the steps in investment casting?
The steps in investment casting include pattern creation, assembly of the pattern onto a wax tree, coating the pattern with ceramic material to form a mold, melting the wax out of the mold, heating the mold to harden it, pouring molten metal into the mold, allowing the metal to cool, and finally breaking the ceramic shell to release the finished casting. Each step is crucial to ensuring the dimensional accuracy and detail of the final product.
What is the pattern of investment casting?
In investment casting, the pattern is typically made from wax and serves as the precise replica of the final part. This wax pattern is placed onto a wax tree if multiple parts are being cast simultaneously. The pattern is dipped in ceramic slurry to create the mold, which will later house the molten metal after the wax is melted and removed. The accuracy of the pattern is critical, as it directly influences the quality of the casting.
What is the sequence of casting process?
The casting process generally follows this sequence: creating a pattern, forming a mold around the pattern, removing the pattern to leave a cavity, pouring molten material into the mold cavity, allowing the material to cool and solidify, and finally breaking or removing the mold to reveal the cast part. In investment casting, additional steps include building the ceramic mold through multiple coatings and removing the wax pattern before casting the metal.
What is the order of the casting process?
The typical order of the casting process begins with the creation of a pattern, followed by mold formation, removal of the pattern (in the case of expendable patterns like wax), pouring of molten material, cooling, and mold removal. In investment casting, this sequence includes pattern assembly, ceramic coating, dewaxing, metal pouring, cooling, and final mold removal. Each step is critical to ensure the accuracy and quality of the cast part.
I love how you’ve personified each alloy like members of a sports team! I’ve always felt like each one has its own strengths, and depending on the job, some perform better than others. Stainless steel is one of my favorites too, especially for its longevity and resistance to corrosion. It really does feel like armor! And you’re absolutely right about titanium – it’s almost futuristic in its capabilities. It always surprises me with its strength-to-weight ratio, especially in aerospace work. Great insights on how these materials have their own stories to tell!
This comparison of choosing materials to a buffet is spot on! Each metal and alloy really does have its own personality, and sometimes you don’t know what you’re getting into until you start working with it. Steel is like the strong, dependable friend, but oh man, aluminum is such a versatile option when you need something lightweight yet sturdy. I recently used aluminum for a bike frame project, and I was amazed at how easily it could be molded while still maintaining strength. But your note about ceramics got me chuckling – so true! They can be amazing, but the moment you take your eye off them… boom, they crack. It’s all about balance and understanding each material’s quirks. Fantastic breakdown, thanks for this walk through the casting “buffet.
Oh, I couldn’t agree more with your take on heat treatment! It’s like the hidden magician behind the curtain, silently enhancing everything. I’ve seen firsthand how it can take a casting from “meh” to top-tier quality, especially in aerospace applications. The reduction of residual stress is a real game-changer when it comes to durability!
Oh man, you really hit the nail on the head about the burnout process! That moment when you’re watching the shell heat up is like holding your breath, hoping everything goes smoothly. I’ve definitely had my fair share of ‘burnout-induced panic’ when a tiny misstep turned into hours of rework. It’s such a delicate balance, like you said. The tension is real when you’re waiting for everything to go right because, as much as we try to anticipate problems, sometimes they just pop up out of nowhere. But hey, when the burnout goes perfectly, it’s like magic! That’s when you can finally exhale and feel like all the effort paid off.
Wow, I couldn’t have said it better myself about ceramic shells being the unsung heroes of casting! They really are the unsung MVPs of the whole process. When I first started working with them, I was amazed at how something so seemingly delicate could withstand such high temperatures. And the finish you get from them? Absolutely flawless! The fact that sometimes you don’t even need to refine the piece after casting is a game changer. It’s true what you said ceramic shells bring both creativity and efficiency, which is the perfect combo in any casting project. Definitely gives us more room to push boundaries with design!
I totally agree with the comparison to sculpting! Investment casting really does feel like an art form, especially when you’re trying to capture those intricate details. I remember the first time I tried the lost wax method it was a mix of excitement and nerves, but seeing the final piece emerge was so worth it. The ceramic shell process always gets me, too. It’s like building a small fortress around your creation! That feeling of breaking it away to reveal the final product is incredibly satisfying, and I love how you captured that ‘cookie cutter’ analogy for pouring the molten metal. Definitely brings back good memories!
The way you talk about wax patterns really resonates with me! There’s something so satisfying about how such a soft, malleable material can define something as strong and permanent as metal. I totally agree with you that the wax pattern is like a tactile blueprint, and it’s incredible how every tiny detail gets carried over into the final product. I’ve had my fair share of moments where a tiny imperfection in the wax has led to a disaster down the line, so I can’t stress enough how important that stage is! It’s funny how something so temporary, like wax, can hold so much power over the final outcome. It’s almost like the wax gives its all and then gracefully steps aside, knowing its job is done. That last line about the wax’s impact being locked into the metal? So true. It’s what makes the whole process feel kind of poetic, really. Great read!
I’ve been fascinated by the wax casting method for years, and you really nailed the explanation here! The way you describe it as sculpting in miniature is so spot on. It’s like you’re creating a little masterpiece, and the fact that every detail, no matter how small, translates perfectly into metal is just pure magic to me. And assembling the wax tree – I’ve always thought of it like setting up a work of art! The whole process is kind of a mix of science and art, which is why I love it so much. I had a laugh when you mentioned the “suit of armor” because that’s exactly what it feels like when you’re coating the wax in ceramic! That step where you melt out the wax never gets old either – it’s like all the anticipation builds up to that moment, and then boom, you’ve got this amazing metal piece. Awesome breakdown!
I absolutely love how you captured the evolution of metal casting in such an engaging way! It’s so easy to forget how long this craft has been around and how much it has evolved from those early, rudimentary methods. I remember learning about the Bronze Age casting techniques in school, and it’s fascinating to think that what they did back then laid the groundwork for the advanced methods we use today. The leap from using basic sand molds to the mechanized processes of the Industrial Revolution is mind-blowing. It really shows the innovation and persistence of the people who worked with metal across the centuries. The fact that casting today caters to industries that need such high precision, like aerospace or medical equipment, just blows my mind. The connection between ancient practices and modern technology is just so seamless when you think about it. It really feels like a tribute to human ingenuity. Thanks for taking us on this journey through history!
I couldn’t agree more! Precision casting truly feels like a blend of art and science. The way it produces complex shapes with minimal waste and stunning surface finishes makes it perfect for industries like healthcare where every millimeter matters.
This is exactly why I love precision casting! It’s such an incredible mix of old-world craftsmanship and cutting-edge tech. I’ve worked on aerospace components, and the level of detail and accuracy you can achieve with this method is astonishing. Plus, you’re absolutely right about it being a financial game-changer. When budgets are tight, precision casting can save so much on material costs. What surprises me most is how versatile it is whether you’re working on a tiny, intricate piece or a large complex part, it just adapts seamlessly. And that feeling of creating something that looks like it was sculpted by hand? It never gets old!
I love how you describe the Investment Casting Process it really is like shaping the future! I remember the first time I saw a wax mold come to life in metal, and it truly felt like magic.