The Basics of Palletised Distribution
When I first figured out the world of logistics, the term ‘Palletised Distribution’ struck me as a puzzle waiting to be solved. This approach is more than just stacking boxes; it’s a finely tuned dance of efficiency and organization.
Picture this: products resting on sturdy pallets, ready to embark on their journey. It’s like a game of Tetris where every piece needs to fit perfectly to ensure smooth transport. In my experience, understanding the nuances of stacked goods distribution can dramatically reduce handling time and streamline operations.
Moreover, the beauty of pallet-based logistics lies in its versatility. Whether you’re dealing with fragile items or bulky machinery, pallets provide a stable foundation. They create a level of consistency that every distribution center craves.
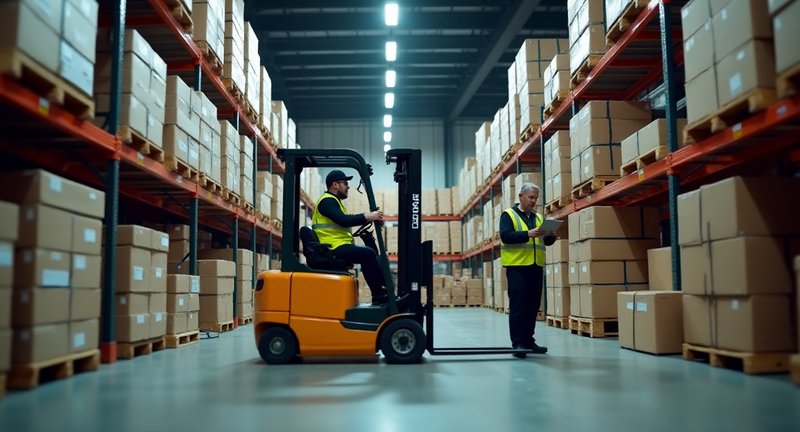
Have you ever noticed how much easier it is to move pallets with a forklift? It’s a game changer. This method allows for quick loading and unloading, which means less downtime for vehicles and happier clients.
Embracing wooden pallet shipping is not just about logistics; it’s a mindset. It invites us to think critically about how we can optimize our processes for better outcomes. When I shifted my focus to this method, I realized it wasn’t just about moving goods it was about creating a seamless experience for everyone involved.
So, if you’re looking to enhance your distribution strategy, consider the myriad benefits of pallet cargo management. It could just be the secret ingredient that propels your business to new heights.
The Efficiency of Palletised Distribution Systems
When we think about efficient delivery systems, there’s a method that often stands out for its balance of speed, cost-effectiveness, and organization. Picture this: instead of scrambling to handle a mountain of individual packages, everything is grouped neatly, making both transport and unloading a breeze. I’ve seen this system transform businesses, saving hours in time and thousands in wasted resources.
One of the reasons for its success lies in how it reduces handling time. Goods are packed and moved in one swift motion. It’s not just quicker it’s safer too. Fewer touchpoints mean fewer chances of damage. This system works wonders, especially for businesses with tight schedules and fragile goods. I remember working with a client who cut their breakage rate by half just by adopting this method.
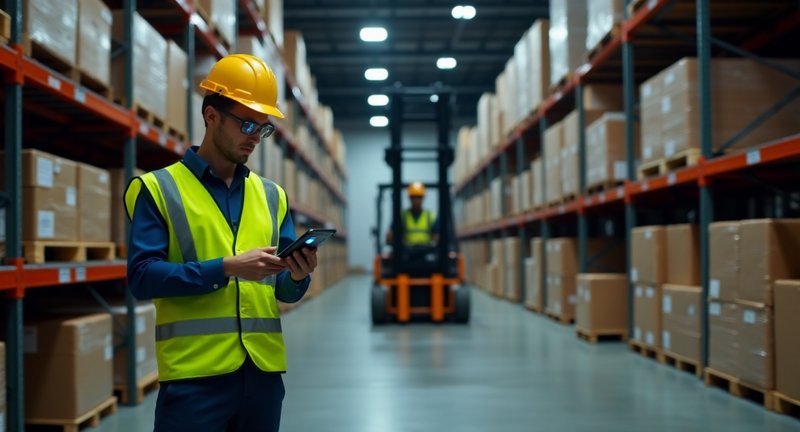
Here are a few key benefits that businesses often overlook:
-
Maximized space utilization: By grouping goods, you can optimize the space in both warehouses and trucks. No more air between packages just full, efficient loads.
-
Reduced labor costs: Since goods are moved in bulk, there’s less need for manual handling. This reduces the number of employees needed and minimizes fatigue-related mistakes.
-
Simplified inventory tracking: Grouping products together streamlines tracking. If you’re running a business, this is a game-changer. It eliminates the headache of scanning and counting every single item.
From my experience, it’s clear that adopting this system not only increases efficiency but also provides a more reliable and cost-effective solution. Think of it as a strategy that clears out the clutter, leaving you more time to focus on the parts of your business that really need attention.
Introduction to Streamlined Goods Handling in Logistics
Streamlined goods handling is at the heart of modern logistics, and it’s much more than simply moving things from point A to point B. From my experience, efficiency in logistics comes down to careful planning and reducing unnecessary steps that slow down the process. When you focus on streamlining, you’re essentially shaving off wasted time, effort, and resources.
One key aspect is understanding how to manage goods in bulk without causing delays or damage. Think of it like this: handling a large volume of goods can feel overwhelming, but if you break it down into smart, efficient chunks, the process flows much more smoothly. Here’s where proper sorting, staging, and stacking techniques come into play:
- Sorting with intent: Organizing goods based on size, weight, or destination allows for quicker access when needed.
- Efficient staging: Placing items strategically for the next step in the process, whether it’s loading or unloading, makes sure there’s no backtracking.
- Smart stacking: Arranging items to maximize space while ensuring safety is crucial to keep everything moving at the right pace.
I’ve seen firsthand how easy it is to get caught up in the daily grind of logistics and miss these small, yet impactful adjustments. But when you implement these methods, the entire flow of goods becomes smoother, and your team’s workload becomes lighter.
Also, it’s about creating a system that feels intuitive. When things are streamlined, your logistics network starts to operate like a well-oiled machine. It’s not just about moving products; it’s about moving them smartly, ensuring both speed and precision in every phase.
The Role of Palletization in Modern Supply Chains
When you think about how goods move around the world, it’s easy to overlook something as simple as a pallet. But trust me, this humble platform is the unsung hero of modern supply chains. From my experience, palletization has transformed how businesses manage logistics, bringing efficiency and cost savings to the forefront.
Think about it. Instead of handling individual boxes, companies stack products on pallets, streamlining operations from warehouses to loading docks. But that’s just scratching the surface. Palletization doesn’t just improve handling it also optimizes space in storage and transport. For example, trucks can be loaded more quickly and with greater precision, reducing idle time and maximizing every square inch of space.
Now, let’s dive into the core benefits:
- Uniformity: Standardized pallets mean fewer headaches. Whether it’s a local delivery or international shipment, using pallets ensures compatibility across transport modes and systems.
- Cost efficiency: Time is money, right? Pallets cut down on the time needed to pack, move, and unload items, which translates directly into savings.
- Safety: Reducing manual handling by shifting goods on pallets minimizes the risk of damage to both the goods and the workers.
- Sustainability: Many companies today are focusing on eco-friendly solutions. Reusable or recyclable pallets contribute to more sustainable logistics practices.
In short, palletization is about more than just moving products. It’s about doing it smartly, safely, and with sustainability in mind. And believe me, when the system runs smoothly, it can feel like magic.
Boosting Efficiency with Pallet-Based Freight Solutions
As for freight solutions, I’ve often found that efficiency is the name of the game. One of the most effective strategies I’ve embraced is utilizing pallet-based systems. Here’s how they can supercharge your operations:
-
Streamlined Handling: Imagine reducing the time spent loading and unloading. Pallets allow for quick and efficient handling, cutting down on labor costs and the risk of product damage. It’s like flipping a switch on your operational speed.
-
Maximized Space: Using pallets ensures that you’re using every inch of your transportation and storage. You can stack items securely, maximizing both vertical and horizontal space. Think of it as playing Tetris with your inventory – the more efficiently you fit things together, the better!
-
Simplified Tracking: In my experience, keeping tabs on shipments can be a headache. However, with a pallet-based approach, tracking becomes far more straightforward. Each pallet can be marked, making it easier to monitor inventory movement and prevent losses.
-
Enhanced Flexibility: The beauty of pallets lies in their adaptability. Whether you’re shipping fragile goods or heavy machinery, pallets can be customized with the right materials and configurations to suit your needs. It’s like having a tailored suit for your freight!
-
Sustainability: With growing awareness around environmental impact, adopting pallet solutions can also be an eco-friendly choice. Many companies now use reusable pallets, reducing waste and contributing to a greener planet.
Incorporating these strategies has not only improved my own logistics but has transformed how I view freight management. By harnessing the power of pallets, you’re not just shipping goods; you’re creating a seamless experience.
Cost-Effectiveness in Bulk Goods Transportation
In the matter of transporting bulk goods, you quickly learn that cost-effectiveness is the name of the game. I’ve found that the key to minimizing expenses is not just about moving items from point A to point B, but about doing it efficiently, keeping operational costs in check, and squeezing every bit of value out of your logistics process.
Here’s where strategy steps in. Let’s look at a few angles that can save time, effort, and, most importantly, money.
-
Optimizing load capacity: This is all about utilizing every square inch of your transportation space. Empty or underused space is essentially wasted money. I’ve seen companies increase profits by simply maximizing truckloads, so don’t overlook the power of full loads.
-
Consolidation of shipments: Bringing multiple shipments together into one larger load can reduce both fuel consumption and handling time. Imagine fewer trips but delivering more goods that’s an efficiency win.
-
Smart route planning: The quickest route isn’t always the cheapest. I always recommend leveraging advanced logistics software that calculates fuel-efficient routes, accounts for traffic patterns, and even monitors weather conditions. This alone can shave significant costs off regular routes.
-
Contracting with reliable carriers: Cheap isn’t always cost-effective. Partnering with trustworthy carriers who maintain their vehicles well and deliver on time can save you from costly delays or damages. A late or damaged shipment often costs more in lost business than any upfront savings.
-
Tracking and real-time monitoring: In my experience, integrating tracking systems ensures timely deliveries and reduces the risks of costly mistakes, like misplaced shipments or unexpected delays.
Bulk goods transportation might seem straightforward, but every small decision contributes to a bigger picture of cost savings.
Enhancing Warehouse Management through Optimized Loading
With regard to fine-tuning warehouse management, optimizing loading strategies is like discovering the secret sauce that can make operations smoother and more efficient. From my own experience, a well-organized loading plan doesn’t just save time; it can be a game-changer in reducing costs and enhancing productivity. Let’s dive into some strategies that have proven to be remarkably effective.
1. Streamlined Loading Procedures
One of the best ways to enhance warehouse management is to create streamlined loading procedures. This involves:
- Segregating Loads: Sort items based on their destination and delivery schedules. This reduces the time spent searching for items during loading.
- Automated Systems: Incorporate automated loading systems where feasible. Automated machinery can increase speed and precision.
- Standardized Processes: Develop standardized loading protocols to ensure consistency and efficiency. This could mean using specific loading sequences or uniform packing methods.
2. Efficient Space Utilization
Maximizing the use of available space is crucial:
- Vertical Space: Don’t just think horizontally; use vertical space by installing taller shelving units. This approach helps in storing more items and making room for efficient loading.
- Flexible Racking Systems: Adjustable racking systems can be reconfigured based on the current load requirements, making them versatile and space-efficient.
- Clear Aisles: Keep aisles clear to allow for smooth movement of loaders and equipment. Clutter-free aisles can prevent accidents and delays.
3. Real-Time Tracking
Implementing real-time tracking systems can revolutionize warehouse operations:
- Barcode Scanning: Utilize barcode scanners for quick and accurate tracking of inventory.
- RFID Technology: Incorporate Radio-Frequency Identification (RFID) tags to monitor items in real time, which can help in reducing errors and streamlining the loading process.
- Inventory Management Software: Leverage software that offers real-time updates on stock levels and loading schedules to make informed decisions.
In essence, optimizing loading procedures not only enhances warehouse efficiency but also contributes to a more organized and responsive supply chain. By focusing on streamlined processes, effective space use, and real-time tracking, you can achieve a well-oiled warehouse operation that stands the test of time.
Reducing Manual Labor with Palletized Freight
In relation to handling large volumes of freight, we all know how daunting manual labor can be. One of the most efficient ways I’ve found to cut down on this exhausting work is by switching to a palletized system. It’s like giving your back a break and letting technology do the heavy lifting.
With goods neatly stacked on pallets, you’re not just organizing cargo; you’re streamlining the entire process. Forklifts glide through the warehouse, taking the burden off people and getting things moving faster. I’ve seen firsthand how this approach can shave hours off daily operations.
What I appreciate most is how it minimizes the risk of injury. Without constant bending, lifting, and shifting of individual items, workers can focus more on strategic tasks. The efficiency boost is real. In fact, it almost feels like cheating watching as an entire pallet moves effortlessly while you stand by.
What’s even more impressive is the flexibility it offers. Whether it’s delicate goods or heavy machinery, this method adapts to your needs. And trust me, once you experience the difference, you’ll wonder why you didn’t make the switch sooner.
Palletised Distribution: A Richly Detailed Overview
When diving into the intricate world of logistics, one concept that frequently garners attention is Palletised Distribution. This approach has transformed the way goods are transported and stored, making it essential for businesses of all sizes. From my own experience, I can attest to the efficiency and organization that palletised methods bring to the table.
Key Advantages of Palletized shipping:
- Enhanced Efficiency: Goods can be moved in bulk, reducing handling time.
- Space Optimization: Pallets maximize storage capabilities, making the most of warehouse space.
- Improved Safety: Reducing manual handling lowers the risk of injury and damage.
- Streamlined Operations: With a standardized system, tracking and inventory management become far more manageable.
In my journey through the logistics landscape, I’ve observed how Palletized logistics not only accelerates delivery times but also enhances the overall reliability of supply chains. It’s fascinating to see how businesses can scale operations by adopting this method. Imagine unloading an entire truckload in mere minutes, as opposed to painstakingly removing items one by one!
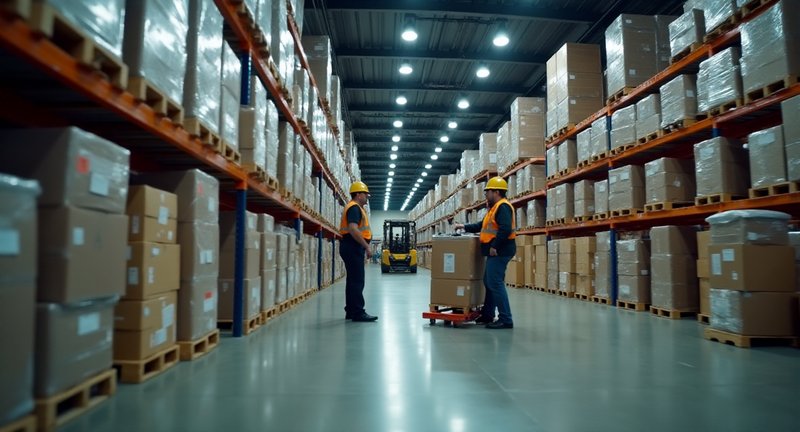
However, it’s not all roses. Companies must ensure they have the right equipment and training in place to handle palletized goods effectively. A well-oiled machine requires not only the physical tools but also the right mindset.
In addition, embracing Palletized freight distribution can be a game-changer for your logistics strategy. If you haven’t yet explored this avenue, consider it. It could very well be the key to unlocking new levels of efficiency in your operations.
Improved Safety Measures in Logistics through Unitized Load Systems
From my experience, one of the most overlooked ways to boost safety in logistics is by using unitized load systems. These systems bring a level of predictability and uniformity to how goods are handled, which has an immediate impact on worker safety.
Imagine this: when you’re working with a well-organized load, the risk of accidents plummets. The goods are stable, less prone to shifting or falling during transit. Trust me, I’ve seen the difference firsthand streamlined systems lead to fewer injuries and safer work environments.
Another advantage comes from the reduced need for manual handling. When goods are bundled into one cohesive unit, there’s less chance for human error. Fewer touchpoints mean fewer opportunities for mishaps. This isn’t just about safety for the workers, but also about minimizing damage to the goods themselves.
I can’t stress enough how much smoother things run when you’re not constantly worrying about the integrity of the load. The mental burden on staff decreases, allowing them to focus more on the task at hand. Safety, at this point, becomes an organic part of the workflow rather than an added responsibility.
From a logistical standpoint, it’s a win-win situation. Not only are your goods moving more efficiently, but you’re also fostering a culture of safety and reliability. The whole process feels more controlled, like you’ve managed to tame an otherwise chaotic environment.
Unitized load systems may not be the first thing that pops into your mind when you think of safety measures, but I can assure you they work wonders.
How Pallet Handling Reduces Risk of Product Damage
When you think about moving large volumes of products, pallet handling isn’t just practical it’s essential. I’ve seen firsthand how it reduces the chances of product damage during transit. Instead of relying on multiple hands, which often leads to human error, pallet handling centralizes everything. It’s a streamlined system, keeping products safe from the chaos of traditional handling.
I can tell you, it’s not just about saving time; it’s about reducing risk. When products are packed on pallets, they move in bulk. This bulk movement protects individual items from being jostled around. Less movement means fewer chances for mishaps, whether it’s a bump in the road or a sudden shift in a warehouse.
If you’re wondering why this matters, think about the costs of damaged goods. Not just the financial costs, but the reputational ones too. With pallet handling, I’ve seen companies avoid these headaches altogether. It’s like putting a shield around your products, ensuring they reach their destination just as they left intact.
Pallets also allow for better stacking, which means fewer products fall or shift during storage. It’s a simple concept but often overlooked. The stability of pallets ensures products aren’t crushed under their own weight. In my experience, this alone can save a business countless hours in rework and replacement costs.
Sustainability Benefits of Palletized Freight Solutions
When we talk about sustainable logistics, palletized freight solutions stand out as a game changer. I’ve seen firsthand how they can transform operations, and not just in terms of efficiency, but for the environment too. So, why does this method deserve more attention?
First off, palletizing shipments optimizes space. By neatly organizing goods on pallets, trucks can carry more with fewer trips, directly cutting down on emissions. Think about it: fewer trucks on the road means less fuel burned. And yes, that’s a win for your bottom line and the planet.
Next, there’s the material advantage. Pallets are typically made from wood, plastic, or metal materials that can be reused multiple times before being recycled. The beauty of this is two-fold: we reduce waste while extending the lifespan of the resources we use.
Let’s break down some key sustainability benefits:
- Reduced Carbon Footprint: Fewer trips mean lower CO2 emissions, contributing to a greener supply chain.
- Lower Energy Consumption: Efficient loading cuts the time and energy needed in handling and transportation.
- Recycling Potential: Pallets can often be repaired, repurposed, or recycled, contributing to a circular economy.
- Waste Reduction: By packaging goods compactly, you minimize the amount of packaging waste and optimize transport loads.
From my experience, these benefits are not only appealing to eco-conscious businesses but are becoming essential as we face increasing environmental regulations. Sustainability isn’t a future goal anymore it’s something we have to act on today. And honestly, switching to palletized freight methods is a simple yet impactful way to start making a difference.
Faster Turnaround Times in Warehousing and Distribution
In my journey through the world of warehousing and distribution, I’ve witnessed firsthand the transformative power of faster turnaround times. Imagine a system where products move with the swiftness of thought, drastically reducing lead times and enhancing customer satisfaction. Here are a few key insights I’ve gleaned that can help streamline operations:
-
Embrace Automation:
- Automated sorting systems can drastically cut down the time taken to process orders.
- Robotics in picking and packing not only boosts speed but also reduces human error.
-
Optimize Layout:
- A well-thought-out warehouse layout minimizes travel time.
- Group similar items together to streamline picking processes.
-
Implement Real-Time Tracking:
- Utilize advanced software to monitor inventory in real time, allowing for quicker decision-making.
- Transparency in stock levels helps prevent delays and miscommunication.
-
Streamline Communication:
- Foster a culture of open communication between teams to address bottlenecks swiftly.
- Regular check-ins and updates can help keep everyone aligned and focused on speed.
-
Regular Training:
- Invest in staff training to ensure everyone is equipped with the latest operational techniques.
- A knowledgeable team can adapt quickly to changes and challenges, keeping the flow seamless.
From my perspective, these strategies don’t just enhance operational efficiency they create a ripple effect of satisfaction throughout the supply chain. So, next time you ponder the rhythm of your warehouse operations, remember that every second counts. It’s about making those seconds work for you!
Enhancing Inventory Control with Pallet Systems
With regard to inventory control, I’ve discovered that an efficient system can truly revolutionize the way we manage stock. One of the standout tools in my experience has been the use of structured stacking and organization techniques.
Imagine walking into a warehouse where everything is neatly arranged on platforms, each item clearly marked and easily accessible. This approach not only saves time but also reduces the chaos that often accompanies inventory management. It’s like a symphony, where each note every product plays its part in harmony.
Incorporating this method has made tracking inventory feel less like a daunting chore and more like a strategic game. Each layer of stacked goods offers a clear view of what’s available and what needs restocking. It’s astonishing how a little organization can enhance clarity and efficiency.
I’ve found that by adopting these innovative systems, businesses can significantly minimize errors and streamline processes. With everything in its place, employees can locate items swiftly, leading to faster order fulfillment and happier customers.
So, if you’re looking to enhance your inventory control, consider embracing this unique approach. Trust me, the results will speak volumes, and your operations will flourish.
Reducing Transit Time with Efficient Load Consolidation
With a focus on reducing transit time, load consolidation is one of the most powerful tools in our arsenal. From my experience, it’s not just about stuffing more products into a single shipment there’s a lot more finesse involved. You need to balance efficiency with speed while ensuring that every inch of space is utilized without overloading. If you’re like me, you’ve probably faced delays because shipments weren’t consolidated properly, and it’s a frustrating experience that could have been avoided.
Let me break it down: proper load consolidation means grouping smaller shipments together to move them as one larger load. What does that mean for transit times? Well, it eliminates the need for multiple trucks or stops, significantly shaving off those crucial hours, or even days. I’ve seen businesses cut their delivery times by as much as 30% by simply streamlining this process.
There are a few strategies I swear by:
- Pre-planning routes and delivery times: Coordinating shipments with other deliveries in the same area.
- Strategic warehouse management: Storing goods in locations closer to their destination.
- Automated consolidation systems: Using technology to identify when and where to combine loads.
It’s not always about throwing more resources at the problem; sometimes, it’s about smarter use of the ones you already have. Remember, the key to reducing transit time is to create fewer trips, not faster ones.
Next time you’re arranging a shipment, consider how you could consolidate better. Trust me, the clock is ticking, and efficiency pays off every time.
Need Help? Hereโs More
What is Palletized logistics?
Pallet-Based shipping refers to the system of transporting goods that are packed and secured on pallets. This method simplifies the handling, loading, and unloading of goods, making the shipping process more efficient and streamlined. Goods are organized on wooden or plastic pallets, ensuring they stay intact during transit. Pallet handling services is widely used in logistics for large shipments, particularly in sectors like manufacturing, retail, and warehousing, where high volumes of products are moved regularly.
What does Palletized mean in shipping?
In shipping, palletized means that goods are placed on a pallet, which is a flat structure used to support the items while they are being transported. By securing goods on pallets, they become easier to handle with forklifts or pallet jacks, reducing the time and labor needed for loading and unloading. This process also minimizes the risk of damage to the products, making it a preferred method for shipping large or heavy items efficiently.
How does pallet delivery work?
Pallet delivery involves placing goods onto a pallet, securing them, and then loading the pallet onto a truck for transport. The pallet, often made from wood or plastic, provides a stable platform that simplifies handling by forklifts or pallet jacks. After reaching the destination, the goods can be unloaded in a similar manner. This system ensures that bulk shipments are handled with care, reducing damage and speeding up the entire process from pickup to delivery.
What are Palletised goods?
Palletised goods are items that are organized, packed, and secured on pallets for transport. These goods can vary in size and type, ranging from boxes of consumer products to large machinery parts. The process of palletizing ensures that the goods are grouped together for easier handling during shipping. By consolidating items on a pallet, it becomes much more efficient to move them using mechanical equipment, reducing the manual labor involved in loading and unloading.
What is palletised delivery?
Palletised delivery refers to the transportation of goods that have been organized and secured on pallets. This method simplifies the logistics process by making it easier to load, transport, and unload large quantities of items. The delivery system often involves the use of forklifts or pallet jacks to handle the pallets, which ensures goods arrive intact and undamaged. Palletised delivery is particularly common for bulk shipments or heavier items that are impractical to move individually.
What does Palletized and non Palletized mean?
Palletized refers to goods that are placed on pallets for transportation, offering a more efficient, secure, and organized way of moving bulk items. Non-palletized goods, on the other hand, are shipped without pallets, often requiring more manual handling and increased care during transport. While palletized shipments are quicker to load and unload with mechanical tools, non-palletized shipments may involve smaller or irregularly shaped items that are handled individually or in smaller packages.
What is the purpose of palletizing?
The purpose of palletizing is to streamline the shipping process by organizing goods on a stable platform for easier handling, storage, and transport. Palletizing makes it quicker to load and unload goods using forklifts or pallet jacks, reducing the need for manual labor. Additionally, palletizing enhances the safety of shipments, as the goods are secured, minimizing the risk of damage during transit. This system improves the overall efficiency of logistics operations, especially for large or bulk shipments.
What is an example of Palletized goods?
An example of palletized goods would be a large shipment of boxed electronics, such as televisions or computer monitors, stacked securely on a pallet and wrapped in plastic. Other examples could include cases of bottled beverages, bulk food products, or construction materials. In each case, the items are grouped together on a pallet to make them easier to transport, reducing the need for excessive manual handling and ensuring they are delivered efficiently.
What does Palletized goods mean?
Palletized goods refer to products or items that are placed on pallets for shipping or storage purposes. These goods are typically stacked or arranged in a way that maximizes space and secured using materials like shrink wrap or straps. Palletizing goods ensures they remain stable and protected during transport, reducing the chances of damage. The use of pallets also simplifies loading and unloading, making the logistics process faster and more efficient.
What is meant by palletizing?
Palletizing is the process of arranging, stacking, and securing goods on a pallet for easy handling and transport. The goods are typically fastened using plastic wrap, bands, or straps to ensure they remain stable during shipment. Palletizing makes it easier to move large volumes of items with mechanical equipment like forklifts, improving the efficiency of loading and unloading. It is a standard practice in industries that regularly ship bulk goods, helping to streamline the logistics process.
How do pallet deliveries work?
Pallet deliveries work by securing goods on pallets before loading them onto a truck or transport vehicle. The pallets are then transported to their destination, where they can be easily unloaded using forklifts or pallet jacks. This system reduces the time and effort needed for manual handling, improves the efficiency of loading and unloading, and ensures goods are transported securely. Pallet deliveries are ideal for bulk shipments, minimizing the risk of damage and speeding up the entire logistics process.
How do you calculate shipping for a pallet?
Shipping for a pallet is typically calculated based on the weight, size (dimensions), and destination of the pallet. Many logistics companies offer pricing based on specific weight categories (e.g., less than or more than 500 kg), and the destination distance can significantly influence the cost. Other factors include the type of goods being shipped, whether special handling is needed, and the delivery method (e.g., express versus standard). It’s also common for freight companies to offer flat rates for standard pallet sizes.
What does delivery on a pallet mean?
Delivery on a pallet means that the goods being transported have been securely packed on a pallet for easier handling and efficient transport. Upon delivery, the pallet is unloaded as a single unit, reducing the amount of time and effort required to handle individual items. Pallet delivery is especially useful for large or bulky shipments, as it minimizes the risk of damage and speeds up the loading and unloading process, making the entire logistics operation smoother.
How does pallet rental work?
Pallet rental works by allowing businesses to rent pallets for a specified period instead of purchasing them outright. Companies rent pallets when they need temporary solutions for transporting or storing goods, and the cost of rental is usually based on the number of pallets used and the duration of the rental. After use, the pallets are returned to the rental provider, who then inspects, repairs, and redistributes them for future use. This system helps businesses save on upfront costs and avoid long-term storage.
Wow, this post really nails it when it comes to optimizing warehouse loading strategies. I can totally relate to the importance of efficient space utilization using vertical space and adjustable racking has been a game-changer for me. I remember when we first implemented RFID tech in our warehouse; it was like flipping a switch on efficiency! The ability to track inventory in real-time not only made things faster but also cut down on so many errors. I also love the idea of keeping aisles clear it’s such a simple tip but can really prevent accidents and save time. This post really highlights the importance of thinking holistically about your warehouse flow. Streamlined loading processes aren’t just about getting things done faster they’re about creating a more resilient and adaptable operation. Thanks for sharing these insights!
You’ve nailed it with the importance of optimizing load capacity. I always tell people that leaving space in a truck is like leaving money on the table. When we started focusing on maximizing every inch of truck space, it made a noticeable difference in our bottom line. Consolidating shipments has been a huge help for us too it cuts down on fuel costs and makes scheduling easier. And, smart route planning? Total lifesaver. We started using software that calculates fuel-efficient routes and even monitors weather changes, and I swear, we’ve shaved off hours from some of our regular trips! Partnering with reliable carriers is another big one. We’ve learned the hard way that going with the cheapest option upfront can cost way more in the long run when things go wrong. Now, we focus on quality and it’s made all the difference. Every small decision, like you said, really does add up to some serious cost savings in bulk transport.
Love the Tetris analogy! That’s exactly what it feels like when we’re stacking pallets. Every inch counts when you’re maximizing space, and it’s so satisfying when everything fits together perfectly. I’ve also found that tracking pallets makes life SO much easier. We’ve had fewer issues with lost inventory ever since we started marking each pallet. It’s almost like a ‘find me’ button for our shipments, which has saved us tons of time and stress. The adaptability of pallets is something I didn’t fully appreciate until we had to ship some fragile electronics along with heavier equipment, and customizing the pallets made it a breeze. Also, the sustainability factor is a bonus I feel good knowing we’re reducing waste. Pallets are truly a freight game-changer, and anyone in logistics who isn’t using them efficiently is missing out big time!
You’re so right about the humble pallet being an unsung hero in the supply chain! I’ve worked in logistics for a while, and it’s crazy how much of a game-changer palletization is. I remember when we switched to using standardized pallets, and it was like night and day in terms of efficiency. Suddenly, everything moved faster no more dealing with boxes toppling over or wasting time rearranging shipments! Plus, the sustainability factor is huge for us. We use reusable pallets, which not only cuts costs in the long run but also helps with our eco-friendly goals. It’s such a simple tool, but without it, I can’t imagine how chaotic things would be. It’s funny how something so basic can make operations run like a well-oiled machine. I totally agree with you, it feels like magic when everything works perfectly, and it’s all thanks to these little wooden (or plastic!) heroes.
The part about breaking bulk handling into smart chunks really hit home for me. I work in a busy distribution center, and this is exactly how we keep things running smoothly. Sorting, staging, and stacking may seem like small steps, but they add up to huge time savings when you’re dealing with hundreds or even thousands of products every day. I’ve definitely seen how focusing on these little details can turn chaos into a well-organized flow of goods. And you’re absolutely right – it’s all about creating an intuitive system. Once you have a solid process in place, everything just clicks into gear. It’s amazing to watch things run like clockwork when the logistics team is on point with these techniques.
This is such a great breakdown of why streamlined delivery systems work so well! I’ve worked in a couple of different logistics roles, and I can’t even count how many hours we saved by switching to a system that groups products together. The point about reducing handling time and improving safety is so true. Fewer touchpoints really do equal fewer accidents and damaged goods. I remember one client who switched to this kind of bulk transport setup and literally slashed their breakage rate, too. And the space utilization! It’s amazing how much more you can fit into a truck or warehouse when everything is grouped properly. It’s one of those things that seems simple but makes a massive difference. Honestly, I think more businesses should be looking into this kind of system if they want to get a handle on their logistics costs and really push efficiency.
Oh man, I can totally relate to that ‘Tetris’ analogy! It’s so true. I work in warehouse management, and palletized distribution really is like a game. Everything has to fit just right for it all to flow smoothly. There’s nothing more satisfying than seeing pallets loaded neatly and efficiently on a truck. It makes everything run so much faster. Plus, the versatility you mentioned is spot on. I’ve handled everything from delicate electronics to industrial machinery, and pallets are a lifesaver every time. Forklifts make moving things around a breeze. I honestly think anyone who isn’t using pallets to streamline their logistics is missing out big time. It’s not just about saving time; it really is about creating that seamless experience for everyone in the supply chain.