Introduction to As Built Survey
In the context of an ‘As Built Survey,’ the importance cannot be overstated, especially in the construction and property development sectors. I’ve worked with enough projects to understand the unique role these surveys play in ensuring everything is accurately documented after construction is complete. You might wonder, why all the fuss about something as simple as recording measurements? Well, here’s why.
An Post-construction survey is essential for comparing the original design plans with the final product. You’re not just working with what was supposed to be done; you’re measuring what actually is done. Often, what we envision on paper is not exactly what happens in reality – and that’s where the survey comes in. It gives you the cold, hard truth, and trust me, that truth is invaluable for everyone involved, from engineers to project managers.
Key aspects covered in an Completed project documentation:
- Exact measurements: The final dimensions of structures, buildings, or land modifications.
- Any deviations: Areas where the construction differed from the original plans, no matter how minor.
- Utilities and infrastructure: Accurate documentation of things like electrical, plumbing, or roadworks, which might have shifted during the build.
You’re basically using it as a tool to make sure all the i’s are dotted and t’s are crossed. It helps avoid future disputes, allows for easier renovations, and gives you a solid record for maintenance. If you skip this, trust me, you’re setting yourself up for a headache later on.
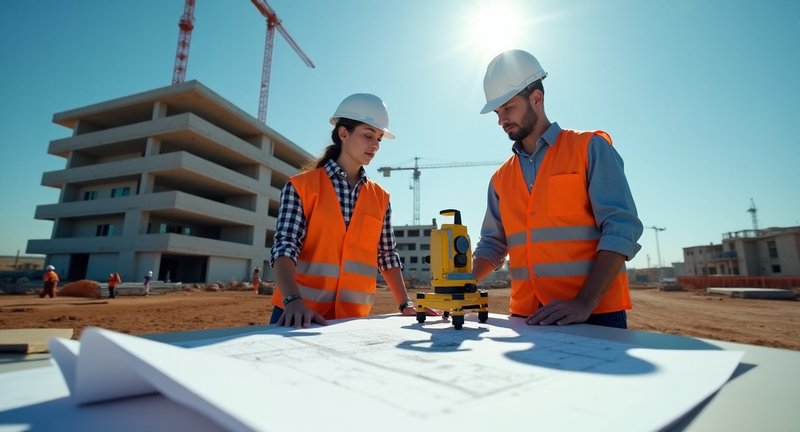
In short, an Final build measurement review is like the final quality check on a project. It captures everything, so when you’re standing in front of your completed building, you know it matches reality.
Understanding the As Built Survey
When you’ve been in construction for a while, one thing becomes crystal clear plans rarely match reality. There’s always some twist. Whether it’s a shifted wall or an unexpected obstacle, the final build almost always deviates from the original blueprint.
That’s where those detailed records of what’s been constructed come into play. It’s like having a map of the terrain you’ve actually crossed, rather than the one you thought you’d hike. You can’t move forward without knowing where you stand now, right?
From my experience, these documents are essential for everyone involved. They help the owner, the builder, and future project managers know precisely what was done. Imagine trying to fix something ten years later without a clue where all the utilities are buried. It’s a nightmare you want to avoid.
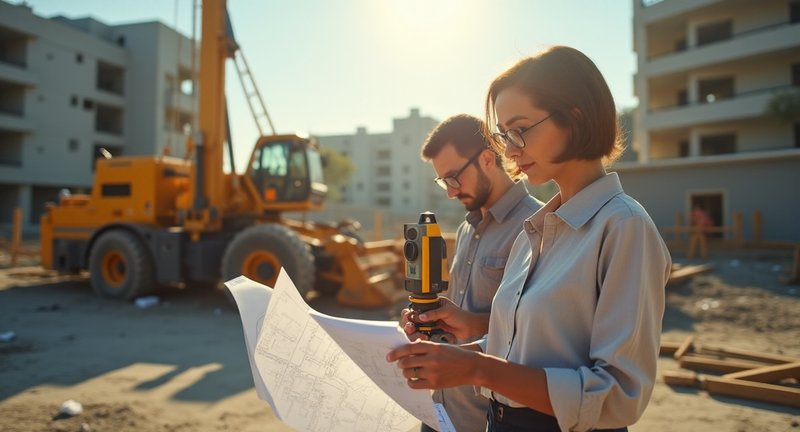
It’s not just about documenting walls and floors; it’s about the whole system, from the electrical layout to the plumbing. In fact, future renovations or expansions rely heavily on the accuracy of these records. If you get this wrong, it’s like setting yourself up for a cascade of expensive surprises.
At the end of the day, you’re not just ticking boxes. You’re building a bridge of trust between the plans and what actually exists on-site. Without this, everyone is flying blind.
What is an As-Built Survey?
When you’re diving into the nature of construction and renovation, you’ll often encounter a type of survey that reveals the truth about a building’s existing state. Picture this: a detailed snapshot of a structure, capturing every nook and cranny just as it stands today. This is the essence of what we’re talking about.
Imagine you’re about to embark on a renovation project. To navigate the twists and turns of your endeavor smoothly, you need a comprehensive record of what’s already there. This record is more than just measurements; it’s a meticulously detailed account of existing conditions. It’s like having a map of a previously unexplored territory.
From my experience, this kind of survey is crucial for avoiding surprises. Whether you’re updating a blueprint or planning a major overhaul, knowing precisely what’s currently in place can save you from costly missteps. It’s your blueprint’s best friend, offering a reality check before any new design takes shape.
In essence, it’s not just about knowing the dimensions of walls and windows; it’s about understanding the real story of the space. This detailed account ensures that your plans are grounded in reality, setting the stage for a successful project.
So, next time you’re gearing up for a construction or renovation project, think of this survey as your best ally. It’s the key to transforming your vision into reality with confidence.
How Construction Documentation Ensures Accuracy
In construction, there’s a saying I’ve come to live by: the devil is in the details. Having worked on a number of large-scale projects, I’ve learned that documentation is the glue that holds everything together.
Imagine trying to build a puzzle without a picture to guide you. That’s what construction would feel like without proper documentation. From the moment the first shovel hits the ground to the final finishing touches, every step must be tracked with precision.
I’ve seen teams stumble when they neglect to document changes made during the build. Construction sites are living, breathing entities, constantly evolving. Keeping track of those changes ensures that nothing falls through the cracks.
Documentation also plays a huge role in avoiding costly mistakes. I’ve had to correct errors before, simply because the original plans were missing crucial updates. Accurate documentation safeguards the entire process, preventing rework and saving both time and money.
It’s not just about checking off boxes. It’s about creating a clear narrative of what happened on-site. I’ve been in meetings where a well-documented project saved the day, offering a concrete timeline and proof of decisions made along the way.
So, while it may not be the most glamorous part of construction, getting the documentation right can make or break a project. If you want things to run smoothly, take it from me: keep those records airtight.
Key Components of Post-Construction Surveys
In the aftermath of construction, there’s a unique responsibility that falls upon surveying. It’s more than just wrapping things up; it’s about ensuring every detail matches the original design intent. I’ve seen firsthand how critical this step is. It’s like giving the project a final once-over before handing it off, but with a precision that leaves no stone unturned.
One of the key elements I always pay close attention to is how the infrastructure aligns with the approved plans. You’d be surprised how easily small deviations can creep in during construction, even when everything seems perfectly orchestrated. This phase of the survey catches those subtle differences, ensuring that nothing goes unnoticed.
Verification of utilities is another essential aspect. The location and functionality of utilities water, electricity, and drainage need thorough checking. Inaccuracies here can lead to serious issues later on, so it’s not just about looking; it’s about understanding the implications.
I’ve also found that detailed measurements of elevation and grading are often overlooked, but they are fundamental to ensuring the land around the building drains properly. Poor drainage can lead to long-term damage, and this is where you safeguard your investment.
In post-construction surveys, it’s about more than accuracy. It’s about accountability, ensuring what was promised is exactly what’s delivered. This is where the real trust between stakeholders is solidified, and I take that responsibility seriously every time.
The Importance of Record Drawings for Projects
As for ensuring the smooth progression and future maintenance of any project, record drawings are a critical tool. Think of them as the final, polished blueprint of everything that’s been built. But, instead of just showing what should happen, they detail what actually did. These drawings are not just about technical accuracy they’re about clarity, transparency, and foresight.
Imagine being a contractor or facility manager down the road and needing to figure out where a specific wire or pipe was installed. Without record drawings, it’s like trying to find a needle in a haystack except the haystack is made of concrete and steel. This is why I always stress their importance.
Here’s what record drawings bring to the table:
- Accurate project reflection: They depict the exact specifications, materials, and placements of everything after construction is done no guesswork involved.
- Enhanced future planning: Whether you’re expanding or renovating, these drawings give future teams a clear map to work from.
- Cost-saving in the long run: They reduce the likelihood of costly mistakes or damages caused by inaccurate assumptions during future works.
- Legal protection and compliance: If there are disputes or regulatory checks, these drawings serve as concrete proof of what was built.
- Simplified maintenance: Maintenance teams benefit immensely from having a visual reference, speeding up repairs and avoiding unnecessary demolition.
In my experience, skipping this step could be a recipe for chaos later on. You may not appreciate their value until you need them and then they become priceless. The reality is, these drawings are the bridge between construction and long-term project success.
Construction Site Verification and Its Role in Compliance
When I think about the intricate dance of compliance in construction, site verification takes center stage. It’s not just a box to check; it’s the heartbeat of a project, ensuring that every beam and bolt aligns with regulatory standards.
Navigating the labyrinth of codes and regulations can feel daunting. However, by diligently verifying the work at hand, we can unveil discrepancies that might otherwise lurk in the shadows, threatening the integrity of the entire project.
In my experience, regular verification serves as a preventive shield. It’s like having a trusted co-pilot who spots turbulence before it escalates into a crisis. Catching potential compliance issues early can save not just time, but also financial resources.
Moreover, this verification process fosters transparency. Clients appreciate being in the loop, and nothing builds trust quite like demonstrating adherence to the rules. It’s a win-win, where everyone walks away feeling secure.
As I reflect on past projects, I can’t stress enough how this diligence has often been the difference between smooth sailing and rocky waters. So, embrace verification as your ally in compliance; it’s the ultimate safeguard in the unpredictable world of construction.
Understanding the Purpose of Final Surveys
When we reach the end of a project, final surveys play a crucial role. They aren’t just about ticking boxes or tying up loose ends; they’re about ensuring the integrity of what has been accomplished.
From my experience, these surveys give us the full picture. They capture the reality on the ground what’s been built or completed compared to what was originally planned. It’s a moment of truth, where you assess not just the surface but the finer details of execution.
What I’ve found fascinating over time is how these surveys reveal insights that often get overlooked during the hustle of a project. They highlight any discrepancies and give a roadmap for corrections if necessary. It’s like having a final checkpoint before officially moving on.
In some ways, I see these surveys as a celebration of the project. It’s a testament to the work done, the challenges overcome, and the milestones achieved. However, they also offer a learning opportunity each project teaches something new for the next one.
Whether it’s identifying areas for improvement or confirming that every detail is in line, the purpose of these surveys goes beyond mere documentation. It’s about making sure the legacy of the project is one of excellence, with nothing left unresolved.
The Role of Field Measurements in Construction
In the bustling world of construction, field measurements play a pivotal role, almost like the secret sauce in your favorite recipe. From my experience, it’s those real-world checks that ensure what’s on paper translates to reality.
Imagine standing on a site where plans come alive. You can almost feel the energy of workers and machinery, but without precise measurements, that energy could quickly spiral into chaos.
Think of it this way: every line drawn on blueprints is merely a wish until you measure it against the landscape. I’ve seen projects stumble when they relied solely on the architect’s vision without grounding it in the tangible world.
It’s crucial to embrace the ground beneath our feet, literally. By collecting accurate field data, we ensure that every beam, every wall, fits snugly into its intended space, avoiding costly rework and delays.
Moreover, these measurements are like a whisper of accountability. They remind us that every project, big or small, must stand up to scrutiny, whether from a team member or an astute client.
In the end, the art of construction isn’t just about creating structures; it’s about crafting realities. And in that craft, field measurements are the unsung heroes, bridging the gap between ambition and achievement.
Why Redlining is Critical for Project Success
When diving into the world of project management, one term that frequently bubbles to the surface is ‘redlining.’ Now, before your eyes glaze over, let me share why this concept is not just a bureaucratic hurdle but a beacon for project success. Trust me, as someone who has navigated these waters, understanding redlining can make or break your project.
So, what exactly is redlining? It’s that meticulous process of reviewing and marking up documents, plans, or drawings to ensure that every little detail aligns with your project’s vision. Here’s why it’s crucial:
-
Clarity in Communication: Redlining allows you to communicate effectively with your team and stakeholders. When everyone can see what’s been changed or needs attention, misunderstandings shrink, and collaboration flourishes.
-
Risk Mitigation: By highlighting potential issues early on, you’re not just playing defense; you’re orchestrating a symphony of proactive solutions. This can save time, money, and a heap of stress later.
-
As Built Survey: A fundamental component of redlining is the ‘Built condition survey.’ This documentation reflects what has been constructed compared to the original design. It’s like a snapshot that helps ensure everything is in its rightful place akin to finding that missing puzzle piece that completes the picture.
-
Enhanced Compliance: In our ever-evolving regulatory landscape, redlining ensures that your project adheres to local codes and standards. Staying compliant means you won’t be blindsided by costly penalties down the road.
In essence, embracing redlining can turn the chaos of project management into a harmonious process. It’s not just about correcting mistakes; it’s about crafting a clear path to success. So next time you encounter redlining, remember, it’s your trusty map guiding you through the complex terrain of project execution.
How End-of-Project Surveys Prevent Future Disputes
I’ve seen firsthand how small oversights can grow into major conflicts. But there’s one tool that often gets overlooked end-of-project surveys. These aren’t just about getting feedback. They’re about setting a solid foundation for the future, especially when things don’t go exactly as planned (and trust me, they rarely do).
End-of-project surveys help to create a clear, documented history of what was delivered versus what was expected. This way, if a client or contractor raises an eyebrow months or even years later, you’ve got an objective snapshot to settle the discussion quickly.
Here’s how these surveys prevent future disputes:
-
Clarify Expectations: They solidify everyone’s understanding of the final deliverables. You’ve crossed the finish line, but was the finish line where everyone thought it would be? This document helps ensure there’s no ambiguity.
-
Track Modifications: Adjustments happen along the way. Changes in scope, materials, or timelines often evolve mid-project. A thorough survey captures those twists and turns, so no one forgets what was agreed upon.
-
Create Accountability: When every stakeholder reviews and signs off on the project’s end result, it becomes much harder to dispute the outcome later on.
From my experience, one of the biggest sources of tension comes from unclear records. A well-crafted end-of-project survey can be a lifeline turning ‘he said, she said’ into ‘we all agreed.’ It’s an easy step that saves you from much harder conversations down the road.
The Benefits of Accurate Built Condition Reports
When diving into the substance of built condition reports, one realizes the transformative power they wield. Having navigated various projects, I’ve witnessed firsthand how these documents serve as a foundational pillar for success.
Accurate condition reports breathe life into a project’s planning phase. They act like a crystal ball, revealing potential pitfalls before they even appear on the horizon. With a clear understanding of a structure’s current state, teams can allocate resources more efficiently, saving both time and money.
From my perspective, the clarity these reports provide can be quite exhilarating. Imagine embarking on a journey armed with a detailed map rather than fumbling in the dark. It allows everyone involved to approach the project with confidence, knowing they are steering clear of unexpected turbulence.
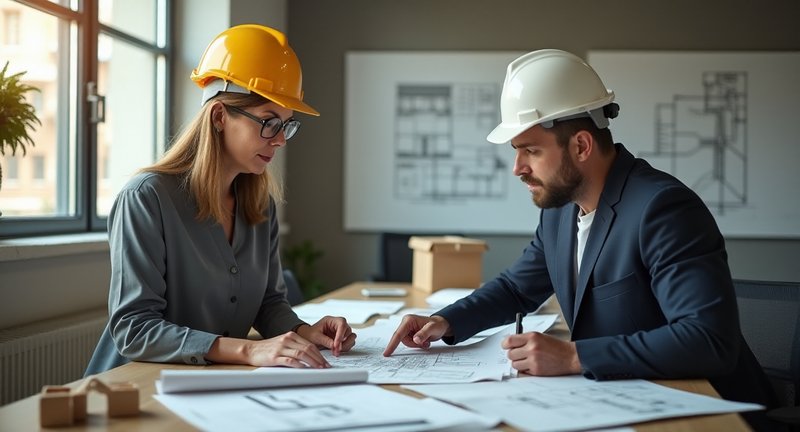
Moreover, these reports pave the way for better communication among stakeholders. When everyone speaks the same language, misunderstandings evaporate. This unity not only fosters collaboration but also ignites innovation, as teams can brainstorm solutions without the weight of confusion holding them back.
And let’s not overlook the invaluable asset of compliance. In my experience, accurate documentation of a structure’s condition is crucial for meeting legal and regulatory requirements. It’s a bit like having a safety net, ensuring that all bases are covered, which can be incredibly reassuring for everyone involved.
In essence, embracing the benefits of precise condition reports can transform a project from a chaotic scramble into a well-orchestrated symphony. With every detail accounted for, the path to success becomes not just a possibility but a palpable reality.
As Built Survey: A Complete Breakdown
When you dive into the world of construction and architecture, there’s a treasure trove of detailed assessments that can make or break a project. Picture this: a meticulous examination of a building’s structure as it stands, rather than how it was originally planned. It’s like peeling back the layers of an onion to reveal the juicy center that everyone wants to get to.
In my experience, this kind of assessment is crucial. It captures the reality of a project and serves as a blueprint for future endeavors. Without it, we’re sailing a ship without a compass unpredictable waters ahead, and the risk of hitting icebergs is high.
Imagine walking through a newly constructed building and seeing the discrepancies between what was designed and what’s actually there. It’s fascinating and sometimes a bit unsettling. You might spot deviations that could affect everything from aesthetics to structural integrity.
One key benefit I’ve noticed is its role in enhancing communication. When all parties are on the same page, it creates harmony. No more “I thought you meant this” misunderstandings. It fosters collaboration and keeps the project moving like a well-oiled machine.
In a nutshell, this detailed analysis isn’t just a box to tick off. It’s a vital component of project management that ensures your vision translates into reality. Embracing it can lead to smoother processes and fewer headaches down the line.
Comparing Design Plans vs. Actual Field Conditions
When you’re working on a project, nothing quite prepares you for the moment when design plans meet the real world. On paper, everything seems clean, calculated, and straightforward. But the truth is, the moment you step onto the field, the game changes.
Field conditions never fail to throw curveballs. Terrain might shift, materials react differently, or environmental factors suddenly matter. You quickly learn that what worked in theory doesn’t always mesh with the gritty reality in front of you.
I’ve had my fair share of experiences where you meticulously follow every drawing, every specification, only to realize the ground doesn’t care about your plans. It’s humbling. You have to adapt, think on your feet, and make adjustments that keep everything flowing smoothly.
There’s a big difference between what’s envisioned and what’s possible. This is where creativity, problem-solving, and flexibility come into play. The ability to reconcile both design and field conditions is what makes or breaks a successful project.
But here’s the kicker: It’s not about scrapping the design altogether. It’s about harmonizing it with reality. You respect the blueprint, but you also respect the land. Finding that balance is the art of construction.
Every project teaches you something new, but this lesson is universal plans are important, but real-world conditions will always have the final say.
How Detailed Site Surveys Enhance Building Safety
When it comes to enhancing building safety, the value of thorough site surveys is often underestimated. From my experience, these meticulous examinations serve as the backbone of a secure construction project.
Imagine stepping onto a site where every crack and crevice has been mapped out. This attention to detail not only highlights potential hazards but also fosters a proactive approach to risk management. It’s like having a treasure map that reveals the hidden gems and pitfalls before you start digging.
Engaging with the data gathered from these surveys is akin to having a detailed conversation with the building itself. Each measurement and note tells a story about the structure’s past, revealing insights that can guide future decisions. This is especially crucial when navigating complex projects where surprises can wreak havoc on timelines and budgets.
Moreover, understanding the existing conditions allows for a tailored design process. When the layout is informed by accurate assessments, architects and engineers can make smarter choices, ultimately leading to safer outcomes. Picture it as creating a recipe with the right ingredients rather than guessing what might taste good.
As you reveal the world of construction, remember that the foundation of safety starts with comprehensive evaluations. Investing in these surveys is like setting up a safety net before the high-flying act begins. Your future self will thank you when you sidestep potential disasters.
Key Questions
What is the as-built survey methodology?
The as-built survey methodology involves the collection of accurate data to document the final condition of a project or structure after its completion. This process includes field measurements, data analysis, and comparing the original design plans with the actual built environment. Surveyors use a combination of technologies such as GPS, laser scanning, or total stations to ensure precise measurements. The goal is to capture any deviations from the original design, reflecting the exact state of the construction at the time of completion.
What is an as-built survey example?
An example of an as-built survey could be a survey conducted for a newly constructed office building. After the construction is complete, a surveyor visits the site to measure and record the location of all structural elements, such as walls, windows, doors, and utilities. These measurements are then compared with the original blueprints to ensure everything is built according to plan or to note any modifications made during construction. This survey can be used for future renovations or legal documentation.
How to make an as-built plan?
To create an as-built plan, first, conduct a comprehensive survey of the completed structure using tools like total stations or laser scanners to collect precise measurements. After gathering the data, compare it with the initial design drawings to identify discrepancies or changes made during construction. Next, update the drawings or CAD models to reflect the actual dimensions and layouts. As a matter of fact, organize and label the modifications clearly to provide an accurate record of the structure’s current condition.
What is the difference between as-built drawings and surveys?
As-built drawings and as-built surveys serve related purposes but differ in scope and detail. As-built drawings are typically produced by the contractor and reflect any changes made during construction, showing the final layout of the structure. As-built surveys, on the other hand, are conducted by professional surveyors to verify that the actual construction matches the design. The survey process involves taking physical measurements, ensuring that all modifications are captured accurately, whereas drawings focus more on the design adjustments.
What are the advantages of as-built survey?
The advantages of an as-built survey include providing an accurate representation of a finished project, ensuring legal compliance, aiding in future maintenance, and facilitating renovations. These surveys help prevent disputes by offering precise records of the construction’s final state. They also serve as essential tools for facility management, allowing future teams to understand the building’s actual layout and any deviations from the original design. Additionally, as-built surveys can help in verifying if all safety and regulatory standards were met during construction.
Is an as-built survey the same as an Alta survey?
No, an as-built survey is not the same as an ALTA survey. An as-built survey focuses on documenting the final condition of a construction project, highlighting any changes or deviations from the original plans. An ALTA survey, on the other hand, is a detailed land survey conducted according to the standards set by the American Land Title Association (ALTA) and is often used for real estate transactions. The ALTA survey includes boundary lines, easements, rights of way, and other relevant information for property ownership and title purposes.
What is an as-built plan?
An as-built plan is a final set of drawings or blueprints that reflect the actual construction of a building or project, showing any changes made during the construction process. These plans include modifications to structural elements, mechanical systems, or site conditions that differ from the original design. As-built plans are essential for future reference, especially for maintenance, renovations, or legal documentation, as they provide a detailed and accurate record of the completed structure.
What is the basic methodology of a survey?
The basic methodology of a survey involves several key steps. First, the surveyor gathers necessary background information, including design plans and site details. Next, they conduct a field survey using tools such as GPS, laser scanners, or total stations to measure distances, angles, and elevations. After data collection, the information is processed and analyzed to create detailed maps or plans. As a matter of fact, the results are compared with design specifications to identify discrepancies or deviations and to ensure the survey’s accuracy.
What is an as-built sample?
An as-built sample refers to a portion of an as-built survey or drawing that demonstrates how final measurements and modifications are documented. For example, a sample could include a detailed section of a floor plan showing the location of walls, windows, and doors as they were actually constructed, compared to their planned positions. This sample provides a clear representation of how the actual construction differs from the initial design, offering a snapshot of the survey process and its results.
What is the objective of as-built survey?
The primary objective of an as-built survey is to provide an accurate, final representation of a completed construction project, reflecting any deviations from the original design plans. These surveys ensure that the project meets all regulatory and design requirements, and they offer valuable documentation for future maintenance, renovations, or property transactions. By capturing the exact dimensions and layout of a structure, an as-built survey helps prevent misunderstandings or legal disputes about the building’s condition.
What is the difference between as-built drawings and surveys?
As-built drawings are typically produced by contractors to document changes made during construction, showing the final layout of a structure. These drawings often reflect minor adjustments that occurred during the building process. In contrast, as-built surveys are conducted by professional surveyors who take precise measurements of the completed structure. While both provide valuable records of a project’s final state, as-built surveys offer a higher level of accuracy and detail by verifying that the construction aligns with design plans.
The way you describe built condition reports is fantastic! I’ve seen how a detailed report can transform project planning into a more focused and efficient process. It’s like having a GPS that shows all the potential bumps on the road ahead. I remember a project where we dodged a major pitfall just because we took the time to create a thorough condition report. This foresight not only saved us time and money but also fostered a sense of teamwork, as everyone was on the same page. Your point about compliance being a safety net is so true; it really brings peace of mind when tackling regulatory requirements. Embracing these reports can indeed elevate a project to new heights!
I completely agree that end-of-project surveys are invaluable! They really help cement expectations and prevent those frustrating “he said, she said” moments later. It’s amazing how a little documentation can save a lot of headaches.
I absolutely resonate with your insights on redlining! It’s a game-changer in project management that I wish everyone understood. I’ve been involved in projects where redlining helped clarify roles and responsibilities, and it dramatically reduced misunderstandings. The proactive nature of this practice is key; it’s like putting on a seatbelt before hitting the road! Plus, that ‘as-built survey’ aspect really nails the importance of aligning actual results with the original vision. It’s comforting to know we have a safety net in place, especially when navigating the complex regulatory landscape. Your analogy about finding the missing puzzle piece is spot on! It truly makes the difference between chaos and harmony in project execution. Keep up the great work sharing these insights!
I love your analogy of field measurements being the secret sauce in construction! It’s such an apt description, and it really highlights how crucial accurate measurements are. I can relate to the energy of a busy site; it’s electric, but it can quickly turn chaotic without that grounding in reality. I’ve been part of projects where everything looked great on paper, but once we started measuring in the field, we realized there were some significant misalignments. It’s like trying to assemble furniture with missing screws you can end up with a wobbly disaster! Your point about accountability is spot on; it ensures that everyone involved stays on their toes. Ultimately, it’s about crafting a solid reality from our ambitious blueprints. Field measurements truly are the unsung heroes! Keep spreading this important message it’s vital for our success in the industry!
Your perspective on final surveys really resonates with me! They truly are the unsung heroes of project completion. I often think of them as a graduation ceremony for a project celebrating the hard work while also providing a reality check. I’ve been part of surveys that revealed surprising discrepancies that we wouldn’t have caught otherwise. It’s fascinating how easy it is to overlook the finer details during the hustle and bustle of construction! Each project teaches us something new, right? I remember one time, a minor oversight during a survey turned into a major lesson for future jobs. The way you described the process as both a celebration and an opportunity for growth really captures the essence of what we do. Here’s to ensuring our legacies are marked by excellence, one final survey at a time!
I absolutely love how you framed site verification as the heartbeat of a construction project! It’s so true; without that diligent oversight, everything can easily fall apart. I’ve seen firsthand how regular check-ins can uncover issues that might not be obvious at first glance. It’s like when you’re baking and realize you forgot the baking powder those little oversights can ruin the whole thing! I really appreciate your point about transparency, too; keeping clients informed fosters trust and makes the entire process smoother. It’s a win-win situation for everyone involved! I remember a project where we caught a compliance issue early, and it saved us from potential chaos later on. Embracing verification isn’t just a good practice; it’s essential for success in this field. Your insights are a great reminder for all of us in the industry!
Record drawings are indeed the unsung heroes of the construction world! They’re not just blueprints; they are a treasure trove of information for anyone involved down the line. I can’t tell you how many times I’ve seen teams flounder without them. Your analogy about searching for a wire or pipe without these drawings is perfect it really puts the importance into perspective. I particularly appreciate how you highlighted their role in future planning and maintenance. It’s true that these drawings save both time and money in the long run. Skipping them is a gamble that often leads to chaos later, and I wholeheartedly agree that their value becomes clear only when they’re needed. They truly bridge the gap between construction and ongoing success!
Your insights on post-construction surveying are spot on! I’ve often marveled at how easily deviations can sneak into a project, even when everything appears perfect. It’s like the construction site has its own personality, and those subtle changes can significantly affect outcomes. I love how you emphasize the importance of verifying utilities; I once encountered a project where a mislocated sewer line created chaos. Attention to detail in surveys truly ensures accountability and trust among all stakeholders. It’s a vital step that’s often overlooked, but you make a compelling case for its necessity!
I absolutely resonate with the saying, ‘the devil is in the details!’ In my own projects, I’ve found that thorough documentation is like having a roadmap in a foreign city it keeps you from getting lost. It’s fascinating how one small oversight can lead to massive headaches down the line. I’ve been in situations where documentation saved the day, helping teams align and clarify decisions. This post perfectly highlights the importance of keeping meticulous records. If only every construction team could embrace this mindset, we’d see way fewer mishaps!
Your insights into the importance of existing condition surveys are spot on! When I started my renovation journey, I was overwhelmed by the potential for surprises lurking behind the walls. Having a detailed survey helped me navigate my project with confidence. It was like having a backstage pass to my home, revealing every little quirk and feature I needed to consider. Not only did it help in avoiding costly mistakes, but it also provided a solid foundation for my new design plans. I wish more people understood how essential these surveys are before diving into renovations! It’s true; this kind of preparation truly transforms a vision into reality and sets the stage for success. Keep advocating for thorough surveying it’s a game changer!
This is such a relatable topic! After years in construction, I can confirm that plans often go awry. I love your analogy of having a map of the actual terrain crossed instead of the intended path! Without those detailed records, it really is like navigating blind. I’ve seen so many projects run into issues because they didn’t have accurate documentation of what was built. It’s always those hidden utilities that bite you in the end! Great reminder for all builders and owners alike.
I completely agree with you about the importance of an ‘As Built Survey’ in construction! I’ve been involved in a couple of projects where we neglected to conduct thorough post-construction surveys, and let me tell you, it turned into a real mess. When it comes to comparing what was intended versus what was actually built, that data is invaluable. Not only does it help clarify any discrepancies, but it also becomes a lifeline for future renovations. Imagine wanting to add an extra room, only to realize that the electrical wiring you thought was in one spot is actually in another! Having those precise measurements on hand saves so much time and hassle. And you’re spot on about it being a final quality check it’s like putting a bow on a gift, ensuring everything is wrapped up neatly. Without it, you’re definitely setting yourself up for potential headaches down the line. Keep spreading the word on this essential practice!