Foreword to Building Steel Price
The ‘Building Steel Price’ is a topic I’ve watched closely over the years, and I’ll be honest it’s far more dynamic than most realize. When you’re dealing with construction or industrial development, the cost of steel isn’t just a line on a spreadsheet; it’s the backbone of entire projects. Steel isn’t a commodity you can afford to overlook. It’s more like the invisible hand guiding your margins.
To start with, the Construction steel cost is sensitive to a variety of factors:
- Global demand and supply shifts: As countries ramp up infrastructure projects or cut back, prices will fluctuate, often unpredictably.
- Raw material costs: Iron ore and coal, key ingredients in steel production, are another set of variables. When these go up, the cost of steel often follows suit.
- Market speculation: Just like oil or gold, steel is subject to the whims of investors and speculators. If there’s a fear of supply chain disruptions, expect prices to spike.
- Environmental regulations: With more focus on reducing emissions, steel production has been affected by stricter policies. That also plays a role in how much you’ll be paying.
What I’ve seen time and again is that those who don’t pay attention to these underlying elements often find themselves caught off-guard. Trust me if you’re looking to get ahead, keeping a finger on the pulse of the Structural steel pricing is essential.
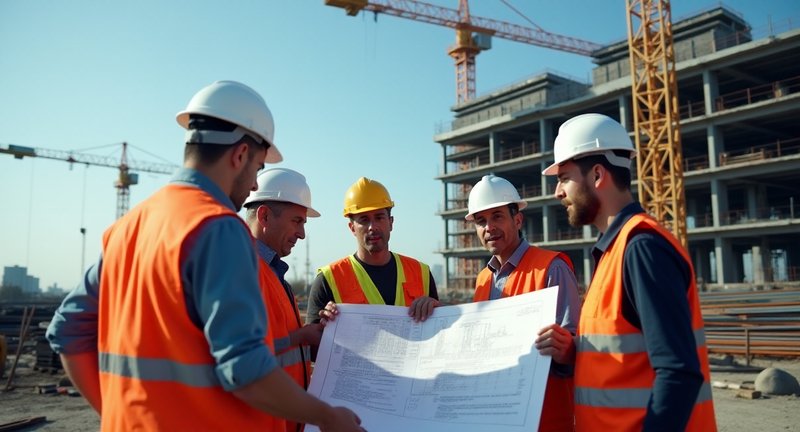
But here’s the thing steel prices are as much about timing as they are about cost. Are you planning a large project soon? You’ll want to keep an eye on these shifts, or better yet, plan ahead to minimize impact.
The Trends of Building Steel Price
Let’s dive into what’s happening with steel costs lately, especially when it comes to construction. If you’ve been keeping an eye on trends, you’ll notice that the cost of steel has been a bit unpredictable – and I can tell you from personal experience, it’s not always easy to forecast. But why is this happening? Well, a few key factors come into play.
First, global demand is a significant driver. Countries like China and India are still consuming enormous amounts of steel, which naturally influences market rates. It’s not just about demand either – the supply chain has seen its fair share of disruptions recently. From logistical bottlenecks to raw material shortages, everything adds up.
Next, we can’t ignore the impact of energy prices. Steel production is incredibly energy-intensive, and with fluctuating costs of oil and gas, producers have to adjust prices to remain competitive. If the energy market spikes, you can bet the cost of steel will follow suit.
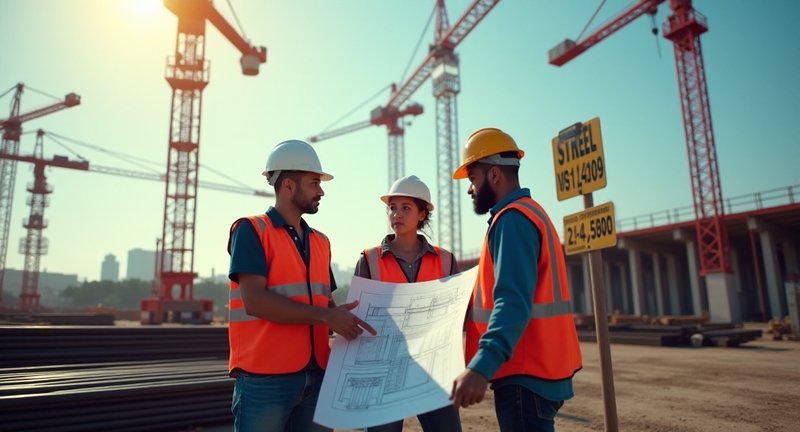
Another major trend? Sustainability initiatives. More companies are moving towards greener production methods. That’s great for the planet, but these eco-friendly changes tend to be more expensive, which, again, is reflected in the final pricing. And trust me, as someone who’s been watching this unfold, it’s not a trend that’s going to slow down anytime soon.
Here’s a quick rundown of what’s influencing steel costs today:
- Global demand shifts, especially in developing nations
- Energy price fluctuations impacting production
- Supply chain disruptions causing delays and shortages
- Increased costs due to sustainable production methods
In short, there’s no simple way to predict the price movement of steel. But by keeping an eye on these factors, we can better understand where things might head.
Introduction to Current Trends in Construction Steel Costs
Steel costs in construction have always been a delicate balance between supply, demand, and economic unpredictability. What’s happening now, though, is truly fascinating. The market is shifting under our feet, and we’ve got to keep an eye on these fluctuations to stay competitive.
In the past year, I’ve watched steel prices dance like never before. This isn’t just due to raw material availability but a blend of global political events and environmental regulations. Supply chain disruptions? Oh, we’ve seen our fair share.
The construction industry is particularly sensitive to these changes. It’s not just about throwing up buildings faster it’s about timing and smart purchasing decisions. I’ve had to adjust project timelines to accommodate unpredictable costs, sometimes on very short notice.
Of course, everyone’s buzzing about new tech, but we can’t forget the core materials. When steel prices go haywire, it ripples through everything, from procurement to project budgets. I’ve found myself rethinking long-standing contracts just to keep up.
But don’t let the volatility scare you. What I’ve learned is that flexibility is key. We must adjust our approach, not only to survive but to thrive in this unpredictable environment.
Factors Influencing the Price of Structural Metal
Considering the price of structural metal, several factors come into play, and they are often more intricate than they initially seem. From my years of observing these markets, I’ve noticed that it’s not just supply and demand at work there’s always something else beneath the surface.
For starters, the raw material cost is a key driver. The price of iron ore, for example, doesn’t just fluctuate because of market trends. It’s influenced by geopolitics, environmental policies, and even natural disasters.
Another factor that many overlook is transportation. Moving heavy metal is no small feat, and the cost of shipping it, whether by land or sea, can shift with fuel prices and logistical challenges. It’s like trying to push a boulder uphill when fuel prices spike.
Let’s not forget labor. A workforce that’s in short supply or under union negotiations can significantly raise production costs, especially in industries as labor-intensive as metal fabrication. I’ve seen projects stalled for months because of wage disputes, which always reflects in the final product’s price.
Environmental regulations are another wild card. A shift in green policies can force companies to invest in cleaner but costlier production methods. While necessary, these changes make structural metal prices anything but predictable.
So, whether you’re watching these markets out of curiosity or because you’re in the middle of a project, it’s a bit like watching the stock market volatile and constantly shifting for reasons both obvious and obscure.
Global Demand and Its Impact on Steel Pricing
When we talk about global demand, it’s more than just numbers on a spreadsheet. Every twist in the world’s economy, from geopolitical shifts to natural disasters, leaves its fingerprint on the steel market. Trust me, I’ve seen how a sudden change in trade policies can turn everything upside down.
Steel isn’t produced in a vacuum. The materials, energy, and labor that go into it are all influenced by the global pulse. When demand in one corner of the world spikes, prices can surge even for those thousands of miles away. I’ve watched prices fluctuate wildly, just because one country decided to ramp up construction.
And don’t think it’s just about supply and demand. No, it’s more intricate than that. The strength of currencies, the volatility in shipping costs, even the cost of raw materials like iron ore – all these factors combine to shape the final pricing. It’s a complex puzzle, and I’ve learned to anticipate shifts, but no one can predict every move.
To really grasp how this works, you’ve got to look at global events in real-time. You learn quickly that when China or the U.S. sneezes, everyone else feels it, especially in markets like steel. The beauty of this business is that it’s always moving, always surprising.
Supply Chain Disruptions Affecting Metal Material Costs
When discussing metal material costs, disruptions in the supply chain are like a ripple in a pond small disturbances can lead to massive waves further down the line. From my experience, several factors are converging to stir up this particular storm. Global logistics bottlenecks, fluctuating demand, and geopolitical tensions are just a few of the culprits wreaking havoc on the availability and cost of raw materials.
The supply chain today isn’t what it used to be. Here’s where the pinch is being felt the most:
- Shipping Delays: The global pandemic left ports congested, and it’s still a major problem. This backlog has pushed up shipping costs, driving material prices skyward.
- Raw Material Shortages: Natural disasters, unexpected plant shutdowns, and political instability in key mining regions have reduced the supply of metals like aluminum, copper, and others used in construction.
- Energy Prices: Metal production is energy-intensive. Spikes in fuel and energy costs have increased production expenses, which inevitably get passed on to buyers like us.
- Currency Volatility: Changes in exchange rates, especially in regions where metals are sourced, add another layer of unpredictability to costs.
In a way, I find this constant flux a real challenge. It’s not just about cost control; it’s about being nimble. Whether you’re managing budgets or planning large-scale projects, it’s important to forecast carefully and keep an eye on market conditions. Materials that were once readily available at a stable price are now fluctuating, sometimes wildly.
Staying flexible, looking for alternative suppliers, or even considering other materials can help mitigate the financial sting of these disruptions. But trust me, this market turbulence isn’t something that’s going to settle anytime soon.
The Role of Inflation in Rising Steel Prices
Inflation is like a sneaky thief lurking in the shadows, quietly eroding the value of your hard-earned money while simultaneously pushing prices skyward. With a focus on the steel industry, the effects of inflation are particularly pronounced. Having watched the fluctuations in steel costs over the years, I can tell you that understanding the intricacies of inflation can provide a clearer picture of why steel prices keep climbing.
Key Factors Influencing Steel Prices Due to Inflation:
-
Raw Material Costs: As inflation rises, the costs of iron ore, coal, and other raw materials needed for steel production also soar. This means that manufacturers have to spend more, and guess what? They pass that expense onto you.
-
Transportation Expenses: Fuel prices are often hitched to the inflation train. As fuel becomes pricier, so do shipping and logistics, further escalating steel costs.
-
Labor Costs: When inflation rears its ugly head, workers demand higher wages to keep pace with the rising cost of living. Steel manufacturers are no exception. Increased labor costs can lead to a direct rise in the price of steel products.
-
Demand and Supply Dynamics: Inflation can create uncertainty in the market, leading to fluctuations in demand. If demand outstrips supply, prices are bound to increase.
-
Government Policies: Inflation often prompts central banks to raise interest rates, impacting financing costs for steel companies. Increased borrowing costs can lead to higher prices as firms look to maintain their profit margins.
In my experience, staying ahead of these inflationary trends requires not just vigilance but also strategic planning. So, next time you hear about rising steel costs, remember that inflation isn’t just a headline; it’s a significant player in the economic theatre.
Impact of Raw Material Costs on Metal Fabrication Prices
Concerning metal fabrication, the cost of raw materials can make or break the budget. I’ve been in situations where you think you’ve nailed down pricing, only to see it balloon because raw material prices decide to take a rollercoaster ride. It’s like cooking a gourmet meal only to realize the price of saffron just tripled. You’re left improvising with turmeric.
Why are raw material costs such a wild card? Well, for one, raw metals are tied to global supply chains and commodity markets. Throw in economic shifts, international trade tensions, or even a surprise mine shutdown, and suddenly the whole game changes. Let’s break it down a little:
- Supply and Demand Dynamics: When a new construction boom hits or a factory in China goes offline, the balance tips. If demand spikes or supply shrinks, you’re in for a price hike.
- Energy Costs: Fabrication is energy-intensive, and when the price of fuel or electricity rises, guess who’s covering that extra cost? Yep, you.
- Transportation and Logistics: Think about it raw metals don’t exactly grow next door. Shipping costs fluctuate, especially when fuel prices jump, and those costs get passed on down the chain.
All this adds up, and before you know it, the cost of metal fabrication skyrockets, and your carefully planned budget needs a serious overhaul. The trick? Staying nimble, keeping an eye on market trends, and honestly learning to pivot when necessary. The good news is that being aware of these factors means you can better predict when the next price hike might hit.
Energy Costs and Their Effect on Steel Manufacturing Prices
Energy costs, often fluctuating without much warning, play a surprisingly hefty role in the pricing of steel. I’ve seen it firsthand – when energy prices surge, so do the costs for steel manufacturers. It’s not just about the production process but the enormous amount of energy required to keep the furnaces burning and the machinery running smoothly.
Have you ever wondered why the ‘Building Steel Price’ can sometimes seem to shift unexpectedly? More often than not, it’s directly tied to energy expenses. When energy providers jack up their rates, steelmakers inevitably pass those costs down the line. It’s a ripple effect that you can almost predict if you know what to watch for.
What’s often overlooked is how manufacturers try to buffer these costs. They tweak production methods, adjust timelines, and sometimes gamble on energy futures. It’s a balancing act that only those deep in the industry truly appreciate, but the result is clear – the ‘Structural steel cost’ won’t sit still when energy prices rise.
You see, the steel industry is like a giant machine, finely tuned but vulnerable to the cost of power. Every kilowatt has a dollar sign attached to it, and I’ve seen how the energy markets can dictate the pace of production. When power prices rise, it’s not just the big, shiny skyscrapers that feel it – it’s every bolt, beam, and bar.
In the end, energy costs are the silent architects behind steel prices, constantly shaping and reshaping what manufacturers charge for their goods. It’s something that, once you notice, you can’t ignore.
Import Tariffs and Their Influence on Steel Prices
With regard to the world of steel, import tariffs are like a double-edged sword. They can create ripples across the entire market, influencing not just the cost of the metal itself, but the broader economic landscape as well.
Imagine you’re navigating a sea of steel prices, with tariffs acting as stormy waves. These tariffs are essentially taxes imposed on steel coming from other countries. When these tariffs go up, the cost of importing steel increases, and this is often passed down the line to manufacturers and consumers alike.
I’ve seen it firsthand how these tariffs can transform the steel market overnight. A sudden spike in tariffs can make steel products more expensive, affecting everything from construction projects to car manufacturing. It’s a classic case of how global policies have local impacts.
On the flip side, tariffs can sometimes protect domestic industries from foreign competition. This might sound like a good deal for local producers, but it’s a balancing act. While it shields them from cheaper imports, it can also drive up costs for everyone who relies on steel.
Navigating this complex landscape requires a keen understanding of both market forces and policy decisions. So, the next time you hear about changes in import tariffs, remember they’re more than just numbers they’re a significant factor shaping the cost of steel and beyond.
Regional Variations in the Cost of Construction Metals
When we dive into the world of construction, one of the biggest financial considerations revolves around the cost of metals. And believe me, it’s not a one-size-fits-all kind of deal. The price of key materials like steel, aluminum, and copper varies widely depending on where you’re located. Let’s take a journey through some of the most significant factors behind these regional price fluctuations.
-
Local supply and demand: In regions where industrial infrastructure is booming, such as parts of Asia, demand for construction metals tends to surge, driving up costs. On the flip side, areas with a surplus of local metal production, like certain parts of Eastern Europe, might enjoy more competitive pricing.
-
Transport costs: Shipping metals halfway across the globe isn’t cheap. The distance from production hubs to your construction site can add substantial costs. A region with easy access to nearby steel mills, for instance, will generally see lower prices than a remote location dependent on imported materials.
-
Currency fluctuations: As construction metals are traded on the global market, exchange rates can be a huge factor. Regions with a weaker currency may see rising import costs for metals, impacting overall project budgets.
-
Environmental regulations: Some regions impose strict environmental regulations on metal production, which can increase the cost of manufacturing. Think of areas like the European Union, where eco-conscious policies mean producers pass those costs down to buyers.
All these factors contribute to a landscape where prices can swing dramatically depending on where you are and what the local conditions are like. If you’re planning a project, it’s crucial to keep an eye on these trends, because being caught off guard by fluctuating metal prices can really throw a wrench into your budget.
A Detailed Analysis of Building Steel Price
Steel is often viewed as the backbone of the construction industry, and its fluctuating cost can send ripples through various sectors. I’ve spent years following the trends, and it’s fascinating how interconnected global events can reshape the landscape.
Take supply chain disruptions, for example. A small hiccup in shipping lanes or a delay at a major steel plant, and you’ll see noticeable shifts in pricing. It’s as if the entire industry is holding its breath, waiting for stability.
Market demand, too, plays a subtle yet critical role. When big projects start popping up like infrastructure initiatives or high-rise developments there’s a surge in demand. And with that comes the inevitable increase in costs, something many overlook when planning their budgets.
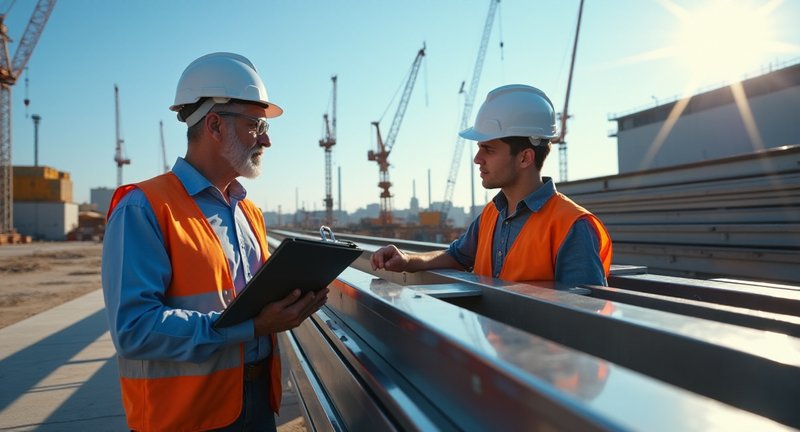
But the real challenge, I’ve found, is in predicting these movements. Even seasoned professionals can be caught off guard when geopolitical tensions, such as trade wars or tariffs, lead to unexpected jumps. It’s like playing chess with an opponent you can’t quite see.
What often goes unnoticed, though, is the impact of technological advances. The industry isn’t static, and innovations in steel production methods can cause shifts, sometimes lowering costs when you least expect it.
By keeping an eye on these factors, one can better navigate the complexities of the market. It’s never a guarantee, but understanding the broader forces at play gives you an edge that many ignore.
Environmental Regulations and Their Effect on Steel Prices
Navigating the labyrinth of environmental regulations can be quite the rollercoaster for those of us in the steel industry. In my experience, these rules often feel like a double-edged sword, striking a delicate balance between ecological responsibility and economic viability.
One major aspect I’ve noticed is how compliance costs ripple through the supply chain. It’s as if every time a new regulation is introduced, the steel market takes a collective breath, anticipating the financial implications.
For instance, stricter emissions standards can lead to increased production costs. This isn’t just a theoretical scenario; I’ve witnessed firsthand how these expenses trickle down, ultimately influencing the prices that consumers face.
Moreover, as manufacturers invest in cleaner technologies to adhere to these regulations, the initial capital outlay can be substantial. These investments may take time to yield benefits, causing short-term price fluctuations that can leave buyers scratching their heads.
Then there’s the matter of consumer demand for greener products. The appetite for sustainable steel is growing, and this trend often leads to a premium on prices. It’s fascinating to see how buyer preferences can steer the market, pushing companies to adapt or risk being left behind.
In the end, environmental regulations are like the weather unpredictable and ever-changing. Understanding their impact on the steel market isn’t just important; it’s essential for anyone looking to make informed decisions in this dynamic landscape.
The Impact of Technological Advances on Steel Costs
In my journey through the world of business and finance, I’ve often marveled at how technology has reshaped industries, and steel production is no exception. The technological advances in this sector have wielded a significant influence over costs, creating ripples that affect everything from construction budgets to global trade. Let’s figure out some key areas where tech innovations have made their mark:
-
Automation: The rise of automation in steel manufacturing has streamlined processes. By implementing robotics and AI, companies are minimizing labor costs and reducing human error, which can significantly lower production costs.
-
Data Analytics: Harnessing data analytics allows producers to optimize their operations. By analyzing supply chain dynamics and consumer demand, firms can make smarter decisions, adjusting production levels and inventory accordingly.
-
Energy Efficiency: New technologies have made steel production more energy-efficient. This not only reduces costs associated with energy consumption but also appeals to environmentally conscious stakeholders.
-
Quality Control: Advanced sensors and monitoring systems enable precise quality control during production. High-quality steel results in lower wastage and fewer returns, directly impacting overall cost efficiency.
-
Research and Development: Investment in R&D has led to the creation of innovative steel grades and composites. These advancements often yield products that require less material without compromising strength, ultimately reducing costs.
Navigating the intertwining paths of technology and steel costs is akin to riding a roller coaster exhilarating, with its ups and downs. As these advancements continue to evolve, they will undoubtedly shape the future landscape of the steel industry, offering new opportunities and challenges along the way.
Forecasting Future Trends in Metal Building Costs
Forecasting future trends in metal building costs is like gazing into a complex kaleidoscope patterns shift, influenced by an array of factors. From my experience, if you want to stay ahead, it’s all about understanding the bigger picture and being ready for change. Here’s what I’ve learned.
First, global economic factors play a huge role. Think about supply chain disruptions, like the ones we’ve seen during major world events. When materials become scarce or harder to transport, costs go up. It’s a ripple effect, and you can’t overlook it.
Then there’s technology. The advancement of prefabrication methods or more efficient recycling processes could impact material costs in surprising ways. Have you noticed how green construction is on the rise? Sustainable practices are not just a trend they’re here to stay, and their costs will trickle down into every aspect of the metal building industry.
Let’s also not forget labor. Skilled labor is becoming harder to find, and when demand outpaces availability, prices climb. It’s one of those things where the market’s shortfall can hit unexpectedly, impacting the overall cost structure.
Here’s a quick breakdown of what to keep an eye on:
- Raw material availability: Natural disasters or geopolitical tensions can reduce access to necessary materials.
- Technological innovations: The introduction of automation or new production techniques can affect pricing over time.
- Sustainability trends: As green construction gains traction, eco-friendly materials may fluctuate in cost.
- Labor market shifts: Shortages in skilled labor can cause delays and push up project costs.
Anticipating these factors will help you better plan for the twists and turns of the metal building industry. Stay agile and always factor in the unexpected.
Answer Hub
Is it cheaper to build with steel?
Building with steel can be more cost-effective compared to other materials depending on the project. Steel is often cheaper because it allows for faster construction, reducing labor costs. Its durability also means lower long-term maintenance costs. However, the total cost depends on factors like building size, design complexity, and local material prices. While steel might have higher upfront costs compared to some alternatives, the overall savings in terms of time and labor often make it more affordable.
Is building with steel cheaper than concrete?
Generally, building with steel can be more cost-effective than using concrete. Steel structures are quicker to assemble, requiring less labor, which can lower construction costs. Additionally, steel’s strength allows for lighter and more flexible designs, reducing the need for extensive foundations compared to concrete. However, specific project requirements, local material availability, and design considerations can influence the cost comparison. Steel offers cost advantages in speed and adaptability, while concrete may be preferable for other reasons such as soundproofing or insulation.
What is the labor cost to erect a steel building?
The labor cost to erect a steel building depends on factors such as location, building size, and complexity. On average, labor can account for about 20-40% of the total project cost. For example, the cost to erect a pre-engineered steel building can range between $3 to $7 per square foot. Skilled labor rates, project duration, and geographical labor rates play a significant role in determining the final cost. Steel buildings generally require fewer workers and less time to assemble, reducing overall labor expenses.
How many square feet is a 40×60 building?
A 40×60 building covers a total area of 2,400 square feet. This size is often used for various purposes like workshops, storage spaces, or small warehouses. The building’s layout can be customized, and the clear span design typical of steel structures maximizes usable space without internal columns. A 2,400 square-foot space can accommodate multiple configurations, making it versatile for different industrial or commercial applications.
Is it cheaper to build with steel or lumber?
Building with steel is often more cost-effective than lumber over time, despite potentially higher initial material costs. Steel provides greater durability, resistance to pests, fire, and environmental damage, leading to lower maintenance and insurance costs. Additionally, steel frames allow for faster construction, saving labor expenses. Lumber, while initially cheaper, can incur more costs in the long run due to required maintenance and susceptibility to environmental damage. Steel is also more eco-friendly and recyclable.
What is the downside of a steel frame house?
One of the main downsides of a steel frame house is its thermal conductivity. Steel is a poor insulator, so additional insulation may be required to meet energy efficiency standards. In some climates, steel frame homes can experience condensation issues if not properly insulated, which may lead to corrosion over time. Additionally, steel frame houses can be noisier due to the material’s acoustic properties, and some may find the initial cost of steel higher than traditional wood framing.
Is it expensive to build with steel?
The cost of building with steel can vary depending on the project size, design complexity, and local material prices. While steel might be more expensive upfront compared to materials like wood or concrete, its benefits, such as durability, faster construction time, and lower maintenance costs, often outweigh the initial investment. Long-term savings on repairs, energy efficiency, and insurance can make steel a more economical choice over time, even if the initial costs are higher.
Is it cheaper to build with steel or concrete?
Steel tends to be more cost-effective than concrete for many projects. Steel allows for faster construction and requires less labor, reducing overall project costs. It is also lighter than concrete, which can result in cost savings for foundations and structural support. On the other hand, concrete might be preferable for soundproofing, insulation, or specific aesthetic requirements. The choice depends on the project’s needs, but steel typically offers more flexibility and lower overall costs.
Is steel structure better than concrete?
Steel structures are often considered better than concrete in terms of flexibility, speed of construction, and adaptability. Steel is lighter, making it ideal for large, open spaces without the need for internal support columns. It’s also more durable, resistant to environmental conditions, and easier to modify or expand. However, concrete offers superior soundproofing and thermal insulation, which might be important for certain projects. The choice between steel and concrete depends on specific project needs, but steel provides more advantages for modern construction.
I couldn’t agree more with your take on environmental regulations being a rollercoaster! It’s such a balancing act between staying compliant and keeping costs down. I’ve seen how stricter rules, especially around emissions, can really shake things up in the industry. But it’s encouraging to see the demand for greener products on the rise feels like consumers are pushing us in the right direction. I guess the challenge is finding that sweet spot where both sustainability and profitability can thrive. Keep the insights coming, really thought-provoking stuff here!
This really hits home for me. The unpredictability of steel prices has been a constant challenge, especially with supply chain issues like you mentioned. I’ve found myself in situations where a minor delay or a sudden geopolitical shift made us rethink entire budgets. It’s a bit like a game of strategy you’re always trying to anticipate the next move, but the rules keep changing. And you’re spot on about technological advances! It’s refreshing when innovation can bring some unexpected cost relief in an otherwise volatile market.
You’re so right about transportation costs being a huge factor in construction! My last project was near a major mill, and the savings on shipping alone made a massive difference. It’s something people often overlook.
I totally agree with your take on tariffs being a double-edged sword! I’ve seen this play out firsthand in the manufacturing world. It’s crazy how a change in policy can ripple through the market and hit every sector along the way. It’s like you’re constantly navigating shifting tides one moment you’re smooth sailing, the next, you’re facing a price spike. The local industries get a boost, sure, but the overall cost for consumers and businesses is tough to ignore. Definitely a complex situation!
I’ve always known energy was a big factor in manufacturing, but this post really hit home just how significant it is in the steel industry. That ripple effect you mentioned, with energy prices affecting every part of the steel production process, makes total sense. I love how you highlight the strategies manufacturers use to buffer costs, like tweaking production timelines or betting on energy futures. It’s a constant balancing act, and it’s amazing how these adjustments influence the final price of structural steel. The next time I see steel prices fluctuate, I’m definitely going to be thinking about how much power it took to produce it. Thanks for shedding light on this!
That comparison to cooking with saffron is perfect! I’ve had a few projects myself where the budget went haywire because raw material costs spiked out of nowhere. It’s frustrating, but your point about staying nimble is key. If you’re in fabrication, you HAVE to roll with the punches and adjust when these price hikes come. Keeping an eye on the global market definitely helps too, especially with the unpredictable nature of supply chains and energy prices. It’s almost like a game of chess – you have to think a few moves ahead. Anyway, thanks for breaking this down in such a relatable way.
It’s crazy how much inflation impacts the steel industry! I’ve been following steel prices for a while, and you’re spot on about raw material costs and transportation. It really makes you think twice when you see prices go up. I’m starting to wonder if there’s any way to predict these trends better, or if it’s all just a guessing game. Great breakdown!
The breakdown of supply chain issues here is spot on! I’ve been struggling with shipping delays ever since the pandemic, and the rising energy prices have made it even harder to stick to budgets. I’ve had to source alternative materials just to keep projects on track, but you’re right – it’s about staying flexible. Keeping an eye on fluctuating raw material prices is now part of the daily grind. It’s tough, but managing this chaos has become a core part of the job these days!
I can totally relate! It’s incredible how a simple policy shift can send ripple effects across the entire industry. I’ve seen prices shoot up overnight just because one country changed its approach to infrastructure.
Totally agree with this! The complexities of pricing structural metal go way beyond simple supply and demand. I’ve worked on projects where delays in raw materials and labor disputes ended up driving up costs massively. And let’s not even get started on the transportation side – shipping heavy stuff gets so pricey when fuel costs jump. It’s crazy how many factors you’ve got to juggle. Keeping up with environmental regulations also adds to the challenge. It’s like a puzzle that never stays the same. Great insights here!
You hit the nail on the head regarding the steel market’s volatility! It’s amazing how external factors like global politics and environmental regulations can impact our bottom line. I’ve had to rethink timelines and budgets so many times that it’s almost become a part of my routine! It’s a challenge, but flexibility truly is our best friend in these situations. Staying adaptable not only helps in managing costs but also positions us to seize opportunities as they arise. Let’s keep pushing for innovative approaches in our industry!
I appreciate this deep dive into steel costs! It’s a topic that deserves attention, especially in today’s fast-paced market. I’ve been in construction for over a decade, and I can relate to the challenges of fluctuating steel prices. It’s a real juggling act trying to balance cost-efficiency with the need for sustainable practices. As someone who’s focused on green building, I find the push for sustainability fascinating but daunting due to the associated costs. With major players like China and India driving demand, it’s hard to keep up. Your mention of energy prices resonated with me too; I’ve seen firsthand how a spike in oil can translate into higher material costs. This isn’t just about numbers on a spreadsheet; it’s about making strategic choices in the face of unpredictability. I’m curious, have you noticed any innovative solutions from suppliers to mitigate these challenges?
I completely agree! The dynamics of steel pricing are often overlooked, yet they can make or break a project. It’s like being on a rollercoaster you have to stay alert to the ups and downs! I’ve found that regularly monitoring these factors not only helps in budgeting but also opens up opportunities for smarter procurement strategies. Great insights here on the invisible forces at play in our industry!