Hyster Forklift Fault Code List
Navigating the world of forklift maintenance can feel like decoding a cryptic message, especially when it comes to fault codes. The is something I’ve had to dive into more times than I can count. It’s like the machine’s way of speaking in its own technical language. Decoding these codes is crucial for keeping operations smooth.
One thing I’ve realized is that understanding this list is not just a technical task but a preventive one. Each code tells a story about what’s going on inside the machine sometimes it’s a minor glitch, other times it’s a warning sign of something bigger. It’s like a mechanic’s secret map to solving problems before they escalate.
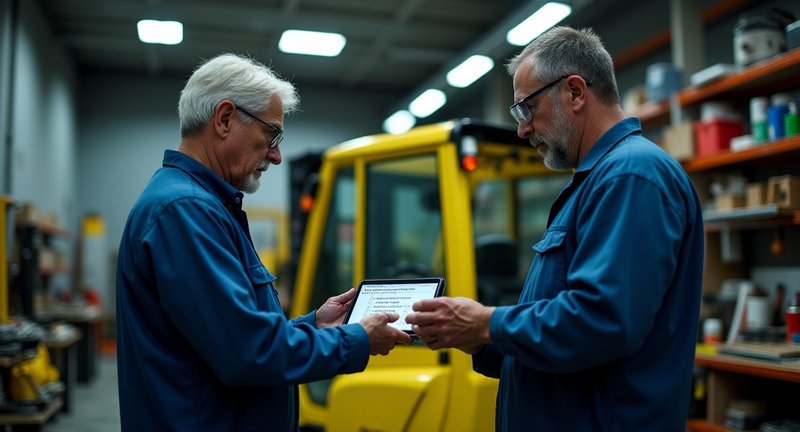
Having the at your fingertips can prevent costly downtime. I’ve been in situations where knowing just one specific code made the difference between a quick fix and a long, expensive repair. It’s not just about fixing what’s broken; it’s about avoiding future breakdowns.
There’s something satisfying about being able to troubleshoot with confidence. That list of fault codes has become my go-to tool for interpreting what my forklift needs. It’s not always easy, but with practice, it becomes second nature. Trust me, once you get the hang of it, you’ll feel like you’re part technician, part detective.
The Importance of Hyster Forklift Fault Code List
Understanding the codes that come up on a forklift is like having a secret language for your equipment. You don’t just fix things; you’re decoding, diagnosing, and getting ahead of potential breakdowns. It’s like being one step ahead of the game, and trust me, that’s where you want to be.
From my own experience, knowing what’s going on under the hood has saved me countless hours of frustration. I’ve seen operators guessing what’s wrong, wasting time and energy on fixes that weren’t even needed. Imagine if you could avoid all that by simply reading the codes and interpreting them correctly.
Forklifts aren’t cheap, and downtime eats away at your productivity. When you’re dealing with fleets, even one machine out of service can disrupt your entire flow. The codes act like a safety net, catching issues before they become costly repairs.
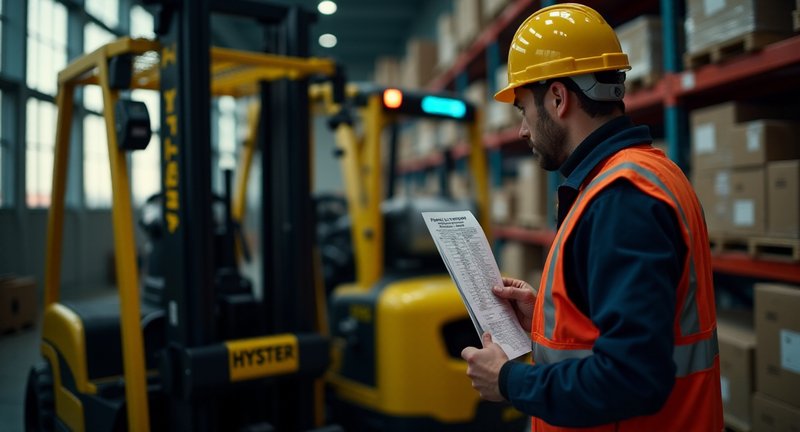
I’ve also noticed that having this knowledge gives you confidence. You’re not just at the mercy of a mechanic; you’re part of the solution. It’s empowering, and that mindset shift is invaluable, especially in high-pressure environments.
When your machine is giving you signals, it’s speaking a language of efficiency and cost savings. Ignore it, and you’re walking on thin ice. But get familiar with what it’s trying to tell you, and you’ll run a tighter, more productive operation. It’s like having a conversation with your forklift, one that could save you big bucks down the line.
Introduction to Forklift Fault Codes
So, you’re dealing with a forklift that’s flashing a fault code, huh? Trust me, I’ve been there more times than I’d like to admit. Forklift fault codes are the machine’s way of speaking up, letting you know there’s something wrong under the hood or, well, under the forks. Whether it’s an engine issue or an electrical fault, these codes save you from playing the guessing game. Instead of scratching your head, you can address the problem quickly.
First off, it’s crucial to understand that not all fault codes are created equal. Some might be minor alerts, like low fluid levels, while others can be more serious, indicating mechanical or electrical failures. Ignoring them is like ignoring the check engine light in your car never a good idea.
Here are a few types of fault codes you might encounter:
- Low Hydraulic Fluid: If your lift isn’t moving as smoothly as it should, this is a common culprit.
- Electrical Malfunctions: Sometimes the code points to wiring or sensor issues.
- Overheating: Temperature sensors are quick to signal if the engine’s getting too hot, often due to clogged filters or coolant problems.
- Transmission Issues: Warning codes here can indicate anything from clutch wear to gear slippage.
If you want to stay ahead of any potential downtime, I recommend getting familiar with your machine’s specific error codes. Each manufacturer may use slightly different terminology or numbering, so it’s worth having a handy reference guide close by. Believe me, it’ll save you a headache in the long run.
And when in doubt, don’t hesitate to call a technician sometimes it’s better to bring in the pros than to tinker around yourself.
Why Fault Codes Matter for Forklift Performance
Forklifts, like any machine, have a unique way of telling us when something is wrong through fault codes. These codes are the language of forklifts, and believe me, when you’ve worked with these machines as long as I have, you learn to appreciate their subtle warnings. Ignoring them is like pretending not to hear your car engine rattle. You might get away with it today, but it’s going to cost you tomorrow.
Each fault code is a key to understanding a specific issue. It could be something as simple as a loose wire or as complex as a failing hydraulic system. But what I’ve learned over the years is that these codes don’t just highlight problems they also save time, money, and prevent bigger issues. The faster you decode and address them, the longer your forklift will run smoothly, which keeps your operations humming along.
You might be tempted to think, ‘Well, how bad can it be to skip checking a code or two?’ Let me tell you: bad. A small glitch in the performance can snowball into significant downtime, impacting your business in ways you won’t see until it’s too late. Staying ahead of faults means staying in control.
To get the best performance from your forklift, you need to treat these codes like gold nuggets. Pay attention to them. Even if they seem minor, they could be the difference between a few minutes of maintenance and days of costly repairs. Forklifts are reliable, but only if you listen when they speak.
Common Issues Signaled by Forklift Error Codes
When you see a forklift flashing error codes, it’s easy to feel overwhelmed. But trust me, those little numbers and symbols aren’t as mysterious as they seem. They’re like your forklift’s way of sending out an SOS telling you exactly what’s wrong, if you know how to decode them.
Some of the most common issues signaled by error codes involve battery health, sensors, and hydraulics. Let’s break this down:
-
Battery Voltage Issues: If your forklift shows an error related to voltage, it’s usually the first hint that your battery isn’t in its prime. You might see a code indicating low voltage, which can cause poor performance, slower lifting speeds, or even shutdowns. I’ve seen it happen ignoring this can lead to more downtime than you’d like.
-
Faulty Sensors: Sensors monitor everything from steering to load handling. If a sensor error pops up, it’s worth giving it immediate attention. Think of it like the nerve system in your body. If one is out of whack, the whole machine could end up performing poorly or even risk damaging goods in transit.
-
Hydraulic Pressure Warnings: If you get a hydraulic-related code, your forklift might be telling you that the hydraulic fluid levels are low, or that there’s a leak somewhere. Skipping maintenance here could leave your machine struggling to lift, which is not a position you want to be in.
In short, error codes aren’t the end of the world they’re more like a cry for help. Learn to listen, and you’ll save yourself from bigger headaches down the road. Your forklift is talking to you, so don’t ignore the conversation.
Understanding Diagnostic Trouble Codes (DTC) in Forklifts
When working with forklifts, it’s essential to understand the language your machine speaks. One of the most important aspects of this is decoding Diagnostic Trouble Codes (DTC). These little codes are like a hidden dialogue between the forklift’s internal system and us, giving insight into what’s going wrong or could go wrong.
From engine misfires to sensor malfunctions, DTCs cover a broad spectrum of potential issues. They serve as an early warning system, alerting operators to underlying problems before they snowball into costly repairs. I’ve learned over time that it’s not just about fixing the code it’s about interpreting the bigger picture.
The trick lies in knowing that not all codes mean immediate danger. Some are mere suggestions for maintenance, while others scream urgency. In my experience, neglecting these codes is like ignoring a quiet knock on the door eventually, it gets louder.
I always recommend staying ahead of the game by regularly checking these codes. It’s surprising how much preventive maintenance can save both time and money in the long run. Believe me, keeping an eye on those little digital alerts pays off big time.
Even if you’re new to forklifts, understanding DTCs is not as daunting as it seems. Once you start recognizing patterns, they almost start to make sense like learning a new language. You don’t need to be a tech wizard, but knowing the basics can go a long way.
How to Read Forklift Error Codes Using Onboard Diagnostics
Reading forklift error codes can feel like deciphering a secret language, but once you know the tricks, it’s much simpler than it seems. Forklifts, especially modern ones, are equipped with onboard diagnostics systems that flash error codes when something’s not right. These codes are like a cry for help from the machine, and the quicker you interpret them, the sooner you can get your forklift back to work.
The first step is to access the diagnostic screen, usually located on the dashboard. Once you’re in, the forklift will display a series of numbers or letters. This might seem overwhelming at first, but don’t worry, each code corresponds to a specific issue. Whether it’s an engine problem, a hydraulic system fault, or something else, the code will point you in the right direction.
In my experience, understanding these codes saves time and money. Rather than waiting for a technician to diagnose the problem, you can take the first steps yourself. Sure, some issues will require a pro, but at least you’ll know what’s going on and be able to communicate it clearly. Plus, the more familiar you get with your forklift’s system, the more confident you’ll be in handling these situations.
One tip I’ve picked up is to keep a notebook handy to jot down the codes as they appear. This gives you a quick reference for future issues. Over time, you’ll start noticing patterns and may even be able to predict problems before they escalate.
Importance of Regular Maintenance for Forklift Error Prevention
When it comes to keeping a fleet of forklifts humming along smoothly, I’ve learned that regular maintenance is not just a suggestion it’s a necessity. You wouldn’t drive a car without oil changes, right? The same principle applies to your forklifts. Think of maintenance as the preventive medicine that wards off ailments before they turn into major issues.
Key Reasons for Regular Maintenance:
- Error Prevention: A well-maintained forklift is less likely to exhibit faults. Regular check-ups allow you to spot potential problems before they escalate into costly repairs.
- Increased Lifespan: Just like any machinery, a forklift that receives proper care will serve you longer. This translates into lower replacement costs and higher ROI.
- Safety Assurance: Faulty forklifts can be dangerous. Regular maintenance ensures that all safety features are operational, protecting your workforce from accidents.
- Improved Efficiency: A finely tuned forklift operates at peak performance, ensuring that productivity remains high. No one wants to deal with unexpected downtime.
In my experience, having a comprehensive Hyster Forklift Fault Code List handy is invaluable. This list helps in quickly diagnosing issues, leading to faster resolutions and minimizing operational disruptions.
Maintenance Checklist:
- Check fluid levels (oil, coolant, hydraulic)
- Inspect tires for wear and tear
- Test brakes and other safety features
- Clean filters and replace as necessary
- Examine forks for cracks or deformities
By sticking to a structured maintenance schedule, you can ensure that your forklifts remain reliable workhorses, ready to tackle the demands of your business. After all, prevention is better than cure, especially in the world of heavy machinery.
Troubleshooting Hyster Forklift Issues
When you’re dealing with Hyster forklifts, you want them to run smoothly and without a hitch. But let’s be honest, they do run into their fair share of problems. Having used them for years, I’ve come across a few common issues and found some solutions that might save you a headache.
Here are some areas to check when troubleshooting:
-
Battery Problems: The number one culprit for sudden stoppages is often the battery. If your forklift isn’t starting, the first thing I recommend is checking the battery connections. Loose or corroded terminals can disrupt power flow. Clean them up, tighten them, and see if that gets the machine purring again.
-
Hydraulic Issues: If the forks aren’t lifting as they should, you might be facing a hydraulic problem. Look for leaks in hoses or seals, and always check the fluid level. Low fluid can affect the forklift’s ability to lift heavy loads smoothly.
-
Engine Overheating: One tricky issue I’ve run into more than once is an overheating engine. Check the coolant levels regularly, and make sure the fan is functioning properly. Sometimes, debris blocks the airflow, causing the engine to overheat.
-
Transmission Trouble: Gear shifting problems can point to transmission wear or low fluid levels. If you notice a sluggish response when changing gears, don’t ignore it. Inspect the transmission fluid and top it off if needed.
The key to diagnosing these issues is not to panic and start with the basics. Trust me, a little preventative maintenance can go a long way. And hey, if you’re still stumped, calling in a technician isn’t a bad idea – better safe than sorry!
A Thorough Exploration of Hyster Forklift Fault Code List
In the world of forklifts, dealing with error codes can be a bit like trying to decipher a secret language. If you’ve ever worked with heavy machinery, you know how crucial it is to have a deep understanding of how everything works, especially when things go wrong. With forklifts, these fault codes are your machine’s way of waving a red flag and saying, ‘Hey, something’s not right here!’
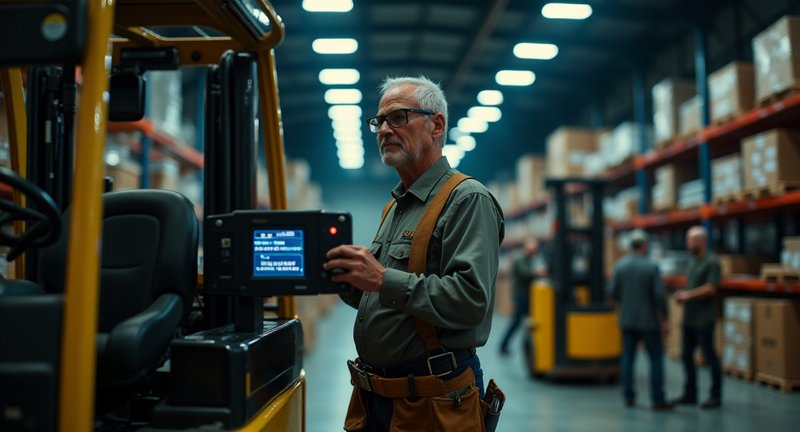
From my own experience, understanding these codes isn’t just about technical knowledge; it’s about efficiency and safety. Every time that little error symbol pops up, it can halt operations, slow down productivity, and even pose potential safety hazards if ignored. So, it’s vital to get ahead of these issues. Let’s break down the key categories you might encounter:
-
Operational Warnings: These codes are generally the machine’s way of telling you there’s a minor issue, like a sensor not working properly. They don’t stop the forklift from functioning immediately, but trust me, you don’t want to ignore them for too long.
-
Critical Faults: When you see one of these, it’s time to pause everything. These codes indicate major mechanical or electrical issues that need immediate attention. Continuing to operate with a critical fault can lead to expensive damage.
-
Maintenance Reminders: Some codes serve as friendly reminders that it’s time for regular service, like oil changes or battery maintenance. If you’re proactive with these, you can save yourself a lot of headaches down the line.
Getting to grips with these messages is like learning to speak forklift. The better you understand, the more efficiently your warehouse or site runs. And trust me, your team will thank you.
Key Error Code Categories in Forklifts
When dealing with forklifts, the error codes can feel like a cryptic language. But over time, I’ve realized there’s a method to the madness. These codes aren’t just random numbers – they break down into specific categories that help diagnose issues quickly.
One category you’ll often see is electrical errors. These might highlight anything from battery problems to wiring faults. Electrical errors are the forklift’s way of telling you it’s not getting the juice it needs, and trust me, ignoring these can lead to downtime you don’t want.
Then, there are hydraulic system issues. These codes usually pop up when something in the forklift’s lifting mechanism isn’t working right. Hydraulics are the backbone of any forklift, and when they fail, it can bring your entire operation to a grinding halt.
Transmission-related errors are another big one. When these codes appear, they often point to mechanical issues with gear shifting or drivetrain. It’s like your forklift telling you it’s having a hard time getting into gear – not something you want to push through.
Each of these categories serves as a clue, guiding you toward the root of the problem. It’s like being a detective for your equipment, and the more familiar you get with these error types, the better you’ll become at keeping your fleet running smoothly.
Solutions to Common Forklift Error Codes
With regard to forklifts, error codes can be a real head-scratcher. I’ve encountered my fair share of these pesky codes, and trust me, they’re not just random numbers; they’re little whispers from the machine, urging you to pay attention.
Take, for instance, the dreaded “E-0001.” This code usually means something’s awry with the battery or charging system. When this pops up, I always make it a point to check the connections and ensure everything is snug. It’s amazing how often a loose wire can create chaos.
Then there’s “E-0003,” which often indicates a problem with the hydraulic system. I’ve learned that checking fluid levels and looking for leaks can save you a lot of headaches down the line. Ignoring this could lead to a rather dramatic and costly repair.
Another common code is “E-0005,” signaling an issue with the controller. I remember my first encounter with this code, and it felt like an ominous storm cloud hovering over my productivity. A quick reset often does the trick, but if it persists, don’t hesitate to consult the manual.
Always remember, deciphering these codes is part art, part science. Each machine has its quirks, and understanding them is essential for smooth sailing. Keeping a keen eye on your forklift and knowing these codes will not only save you time but also keep your operations running like a well-oiled machine.
Electrical System Error Codes and Their Meanings
When dealing with electrical system error codes in forklifts, it’s akin to deciphering a complex puzzle. Each code serves as a lifeline, guiding you through potential issues lurking in the shadows of your machine. From my experience, understanding these codes can be the difference between a minor hiccup and a major breakdown.
Common Electrical System Error Codes:
-
E1 – Communication Error
This indicates a disconnect between the truck’s control system and the operator’s interface. It might be a loose connection or a deeper issue needing immediate attention. -
E2 – Battery Voltage Low
When you see this, it’s time to check your battery’s health. A low voltage could signal that the battery is nearing the end of its life or simply needs a good charge. -
E3 – Motor Overcurrent
This code pops up when the electric motor is pulling more current than it should. It could be due to excessive load or even a mechanical jam. -
E4 – Temperature Warning
A red flag! This code means the forklift’s electrical components are overheating. Allow it to cool down before further use to avoid damage. -
E5 – System Voltage High
If this shows up, you might want to examine your power supply. High voltage can wreak havoc on electrical systems.
Tips for Handling Error Codes:
- Document Everything: Keeping a log of codes and actions taken can save time down the road.
- Regular Maintenance: Like any machine, a forklift thrives on care. Routine checks can prevent many errors.
- Seek Professional Help: Don’t hesitate to call in an expert if a code seems out of your depth. Better safe than sorry!
Understanding these codes doesn’t have to be a daunting task. With a bit of patience and practice, you’ll be troubleshooting like a pro in no time.
Hydraulic System Error Codes in Forklifts
In my years of experience, hydraulic system error codes can feel like cryptic puzzles. These codes, though frustrating at first, are essential messengers, trying to tell us what’s wrong beneath the surface. With regard to forklifts, these messages can indicate anything from a minor pressure imbalance to a significant system failure.
One of the most common scenarios I’ve encountered is a forklift suddenly losing power. Hydraulic error codes often hold the key. A glance at the system’s digital readout can save hours of guessing and manual inspections. Think of it like a shortcut to the heart of the issue.
The tricky part is that not all codes are created equal. Some may signal a simple fix, such as low fluid levels, while others point to more complex problems, like pump malfunctions. Each code acts like a breadcrumb, leading you closer to the solution if you know how to read it.
What I’ve learned is that becoming familiar with these codes isn’t just useful, it’s crucial. It’s the difference between a few minutes of downtime and a full day lost to troubleshooting. Even the most reliable forklifts can surprise you with an unexpected code now and then.
So, the next time your forklift throws out a hydraulic error code, don’t panic. Take a breath, grab the manual (or a trusted guide), and let the code do the talking. Understanding what it’s telling you can be the fastest way back to smooth operation.
Engine-Related Error Codes for Forklifts
Regarding engine-related error codes for forklifts, it’s like deciphering a secret language. I remember the first time I encountered a cryptic code flashing on the dashboard; I felt like I was on a treasure hunt, but instead of gold, I was after a solution.
These error codes can range from the mundane to the perplexing. For instance, a simple code might indicate a low fuel level, while others can reveal complex issues, like a malfunctioning ignition system. Each code acts like a whisper from the engine, hinting at what’s amiss.
It’s essential to take these signals seriously. Ignoring a minor code could lead to a major breakdown, costing both time and money. I’ve learned to keep a handy guide something to quickly translate those mysterious flashes.
Investing in diagnostic tools has been a game changer. These gadgets not only read error codes but also provide insights into the forklift’s overall health. It’s like having a mechanic right in your pocket!
And don’t underestimate the power of regular maintenance. Keeping your forklift in top shape often means fewer codes popping up. After all, prevention is the best medicine, isn’t it?
In my experience, understanding these codes has transformed how I manage equipment. It’s not just about fixing issues as they arise; it’s about fostering a proactive approach to forklift care. Trust me, it pays off in the long run!
Find Your Answer
How to check codes on a Hyster forklift?
To check codes on a Hyster forklift, start by turning on the forklift’s ignition without starting the engine. Use the diagnostic panel or LCD screen to display error codes, which may require pressing specific buttons or navigating through menus, depending on your model. The error code will often appear as a combination of numbers and letters. These codes indicate specific issues within the forklift’s system, helping technicians identify problems quickly. Refer to your forklift’s manual for detailed steps as models vary.
How do you clear a forklift error code?
Clearing a forklift error code typically requires diagnosing and fixing the underlying issue first. After resolving the problem, turning the forklift off and on may reset the error code. In some cases, you may need to access the control panel or use a diagnostic tool to manually clear the code. If the error persists, a professional technician may need to perform a software reset. Always consult the operator’s manual for specific instructions based on your forklift model.
How to fix Hyster code 1239 1 forklift?
The Hyster code 1239-1 usually relates to a lift system issue or hydraulic fault. First, check the hydraulic fluid levels and ensure the system is free of air. Examine the hydraulic hoses, fittings, and cylinders for any leaks or damage. If there is a mechanical issue, such as a damaged valve or piston, repair or replace the affected parts. If the problem persists after addressing these, you may need a diagnostic tool or technician to investigate further and reset the error code.
What is the Hyster fault code 524245 4?
Fault code 524245-4 on a Hyster forklift often relates to a communication error within the forklift’s CAN bus system, which controls the electronic systems. This could indicate an issue with the electrical connections, wiring, or one of the sensors. Start by inspecting the wiring harnesses and connectors for damage or loose connections. If no physical damage is detected, a diagnostic scan tool may be required to identify the faulty sensor or module that needs repair or replacement.
Where is the diagnostic port on a Hyster forklift?
The diagnostic port on a Hyster forklift is typically located near the engine compartment, close to the control unit or under the dash panel near the operator’s seat. This port is used to connect diagnostic tools for reading fault codes and checking system statuses. The exact location may vary depending on the forklift model and year, so it’s recommended to consult the forklift’s user manual or look for an OBD-style connector.
How to clear fault codes on a Hyster forklift?
To clear fault codes on a Hyster forklift, first, address the issue that caused the fault. Once the problem is fixed, turning the ignition off and then back on may reset the code. If this doesn’t work, you may need to use a diagnostic tool connected to the forklift’s diagnostic port. Certain models also allow for manual code clearing through the control panel or by entering specific sequences via the display interface. Always consult the manual for model-specific instructions.
How do I identify my Hyster forklift engine?
You can identify your Hyster forklift engine by checking the engine identification plate, which is typically mounted on the engine itself. The plate includes vital details like the engine model, serial number, and manufacturer. If the plate is worn or missing, check your forklift’s manual or use the serial number of the forklift, which can be found on the chassis or data tag, to trace the engine information via the manufacturer or dealer.
What is the code 522655 on a Hyster forklift?
The code 522655 on a Hyster forklift typically indicates an issue related to the hydraulic pressure system, such as low hydraulic pressure or a fault in the pressure sensor. Inspect the hydraulic fluid levels and ensure the hydraulic pump is functioning properly. Additionally, check for leaks or blockages in the system that might be causing a pressure drop. If necessary, replace the sensor or repair any mechanical components, then reset the fault code using diagnostic tools.
How do you clear codes on a forklift?
To clear codes on a forklift, fix the underlying issue causing the error code. Once resolved, restart the forklift by turning the ignition off and on to see if the code disappears. For persistent codes, some models may require you to access the diagnostic system or use an external diagnostic tool. If you’re unable to clear the code, professional service technicians can manually reset the system or address deeper electronic issues.
How do you clear fault codes?
Clearing fault codes involves first diagnosing and repairing the cause of the fault. After resolving the issue, power cycling the forklift (turning it off and then back on) can reset the code on many models. If the code remains, you may need to access the onboard diagnostics system or connect a diagnostic scanner to the forklift’s port. Follow the manufacturer’s specific procedures, as some codes can only be cleared using specialized software or tools.
How to reset Hyster fault code?
To reset a Hyster forklift fault code, fix the issue that triggered the code first. Then, turn off the ignition and restart the forklift to see if the code clears. If the error persists, use the diagnostic panel to enter reset commands or connect a diagnostic tool to the forklift’s diagnostic port. Some Hyster models may also allow manual clearing of codes by navigating through the control interface. Always consult the user manual for model-specific reset instructions.
What does E-23 mean on a forklift?
The E-23 code on a forklift typically refers to an issue with the transmission system, often related to the temperature or operation of the transmission fluid. Check the fluid levels and quality, ensuring that the transmission fluid isn’t overheating. Low fluid levels or old, degraded fluid can trigger this code. Address the fluid levels or replace the fluid if necessary. If the issue persists, the transmission system may require further diagnostics or mechanical repair.
I completely relate to the struggle of decoding those pesky electrical error codes! It really is like piecing together a puzzle where every clue matters. I remember the first time I saw the E1 code flash on my forklift’s display. I panicked, thinking it might be something catastrophic, only to find out it was just a loose connector. Documenting everything, as you suggested, has become my go-to strategy. It not only saves me time but also helps in tracking recurring issues. And regular maintenance? Absolutely! Just like our bodies, forklifts need a little TLC to keep running smoothly. My mechanic always emphasizes that a stitch in time saves nine, and I’ve seen that firsthand. The tips you shared are invaluable for both newbies and seasoned operators alike. It’s empowering to know that with a bit of practice and patience, we can turn a frustrating experience into a manageable one. Keep up the fantastic work in demystifying these codes for everyone!
This is such a relatable post! I’ve definitely had my fair share of code confusion while operating forklifts. ‘E-0001’ and ‘E-0003’ are familiar friends at this point, and I appreciate your tips on addressing them! The reminder about checking connections for E-0001 is golden loose wires are like sneaky gremlins! As for E-0003, I couldn’t agree more about the importance of regular fluid checks; I learned that the hard way too! It’s fascinating how understanding these codes really does turn into a sort of art and science. It makes the job more engaging, don’t you think? Thanks for sharing your experiences and insights; they really help demystify these pesky codes!
Your post really hits home for anyone who’s had to grapple with forklift error codes. It’s almost like being a detective in the warehouse! I love how you categorized the errors, especially the electrical ones. The first time I encountered an electrical error, I learned the hard way not to ignore it. I ended up with a dead battery during a critical delivery, which was quite the headache! Hydraulic issues are another critical area; I’ve seen operations come to a halt due to a simple fluid leak. It’s incredible how these little clues can guide us to the root of the problem and keep things moving. Your approach to understanding these codes as a helpful guide rather than a nuisance is refreshing! Keep sharing these insights; they’re invaluable!
I couldn’t agree more with your take on forklift error codes! They really do feel like a secret language, especially when you first encounter them. In my experience, it’s so important to be proactive about these warnings. I remember the first time I saw a critical fault code pop up it felt like a scene out of a horror movie! The tension in the warehouse was palpable. Thankfully, I had just attended a training session about deciphering these codes, which saved the day. You mentioned operational warnings, and I completely echo that sentiment. They may seem minor, but overlooking them can lead to major headaches later. It’s a classic case of ‘an ounce of prevention is worth a pound of cure.’ Plus, getting familiar with the error codes does feel a bit like being a mechanic wizard! The more you learn, the easier it becomes to keep everything running smoothly. Thanks for breaking it down so clearly!
Your tips on troubleshooting common issues with Hyster forklifts are super helpful! Battery problems can indeed be a major headache. I had a situation where my forklift wouldn’t start, and after panicking for a bit, I remembered your advice and checked the battery connections. Sure enough, the terminals were loose! I also appreciate your insights on hydraulic and overheating issues. They can be tricky to diagnose without a solid checklist. I’ve learned that a little preventative maintenance like regularly checking fluid levels can save a lot of time and frustration. Plus, who doesn’t enjoy a smoothly running forklift? If I could add one more tip, it would be to keep a spare battery on hand for those unexpected moments. Thanks for sharing your experiences; they’ve really made a difference in my approach to forklift maintenance!
I couldn’t agree more with your emphasis on regular maintenance it’s truly the backbone of forklift longevity! Just like you said, it’s like preventive medicine for our machinery. I’ve seen firsthand how skipping maintenance can lead to cascading issues down the line. My go-to practice is to create a maintenance calendar that alerts me when each task is due. This way, I never forget those crucial checks, and I can avoid those dreaded emergency repairs. Plus, it’s such a relief knowing that I’m doing my part to keep my team safe. The checklist you provided is a fantastic resource too I’ll definitely be using that moving forward! Here’s to keeping our fleets running smoothly!
I completely relate to the struggle of understanding forklift error codes! It can definitely feel like trying to crack a secret code at times. Your suggestion to keep a notebook handy is brilliant I’ve started doing that myself, and it’s made a world of difference! Not only can I reference past issues, but I also feel more prepared when I need to discuss problems with my technician. It’s empowering to have that knowledge at my fingertips. Thanks for sharing these insights; they really help demystify the diagnostic process!
Your discussion on Diagnostic Trouble Codes is both informative and engaging! I love how you’ve compared DTCs to a hidden dialogue what a great analogy! I’ve always viewed these codes as intimidating, but your perspective helps me see them as friendly reminders instead. I had a misfire issue once, and it was a real headache because I didn’t recognize the DTC early enough. Your tip about distinguishing between urgent and maintenance codes is so crucial! I think it’s fantastic that you encourage newcomers not to feel overwhelmed. Learning to read those codes really is like picking up a new language, and it can empower anyone working with forklifts. I’ll definitely be more proactive in monitoring my machine’s health from now on. Great job!
Wow, your breakdown of the error codes is spot on! I used to panic whenever I saw those flashing lights on my forklift dashboard, thinking it meant disaster. But realizing they’re like a little voice of reason from the machine makes all the difference. Your examples about battery voltage and faulty sensors really resonate with me. I once had a situation where I ignored a battery warning, and my forklift ended up crawling like a turtle! Now, I make it a point to check those codes regularly. It’s like having a conversation with the machine instead of just being the operator. Plus, a little bit of preventive maintenance can save so much time and stress in the long run. Thanks for breaking it down so clearly; I’ll definitely share this with my team!
I absolutely love how you’ve articulated the importance of fault codes in forklifts! Having worked in warehousing for a few years, I can attest to the fact that these codes are like our machines’ way of sharing their concerns. Ignoring those little flashes is indeed a gamble. One time, I overlooked a minor hydraulic warning, and it led to an unexpected breakdown that caused major delays. Your advice about treating these codes like gold nuggets really hits home! It’s like preventative care for our machines, and in the long run, it keeps everything running smoothly. Thanks for sharing such valuable insights!
Oh, I can totally relate to that feeling of frustration when a forklift throws a fault code at you! It’s like having a surprise quiz that you didn’t study for. I appreciate how you emphasized that not all fault codes are created equal. I once ignored a minor code, thinking it would just go away, and boy, did I regret it! It turned into a major issue that put our operations on hold for days! Now, I make it a point to keep a reference guide handy and even jot down the common codes we encounter on a sticky note next to our maintenance log. It’s helped me become the go-to person for quick troubleshooting in our shop. Plus, who doesn’t love that feeling of knowing you’re one step ahead of potential disasters? If anyone reading this hasn’t yet dived into their machine’s manual, I highly recommend it! It’s like having a backstage pass to understanding your equipment better. And yes, when in doubt, always call in the pros better safe than sorry! Keep up the informative posts
Absolutely! You hit the nail on the head with the idea of having a secret language for forklifts. Understanding those codes is like having a superpower! I remember when I first started, I felt overwhelmed by the technical jargon. But as I began decoding the messages from my machine, it felt like unlocking a whole new world of efficiency. That moment when you confidently call out a fault code and see the relief on your coworkers’ faces is priceless. It really does save time and energy in the long run! Keep sharing those insights; they are invaluable!
Navigating the labyrinth of forklift maintenance can indeed feel daunting at times! I completely agree with you about the importance of understanding those fault codes. They are like little signals from our machines, each one telling a story about its health. I’ve had my fair share of ‘mystery breakdowns,’ and let me tell you, having that knowledge at hand truly makes a difference. The analogy of being a technician and a detective is spot on! It’s a real confidence booster when you can troubleshoot and know that you’re preventing bigger issues down the line. Plus, it’s quite satisfying when you can share your insights with coworkers, empowering them to tackle issues head-on. Just the other day, I decoded a fault code that saved our team hours of downtime, which feels amazing! Keep up the great work of spreading this knowledge; it really helps everyone in the long run!