Foreword to Warehouse Shipping
‘Warehouse Shipping’ – now that’s a phrase that opens the door to logistics mastery. When I first ventured into the world of warehouses, I quickly learned it’s not just about moving boxes from point A to point B. It’s about orchestrating a well-tuned machine, where every piece of the puzzle has to fit perfectly.
I remember the first time I had to oversee a large-scale shipment from the warehouse. What stood out was how much planning went into the process – way more than I imagined. It’s like conducting a symphony, but instead of violins and cellos, you have forklifts and inventory management systems. Timing is everything.
As I delved deeper, it became clear that ‘Distribution center logistics’ is the backbone of any supply chain. You have the product, but getting it out the door and to the customer efficiently is where the magic happens. If one thing goes awry – even a small delay – the whole operation feels the ripple effects.
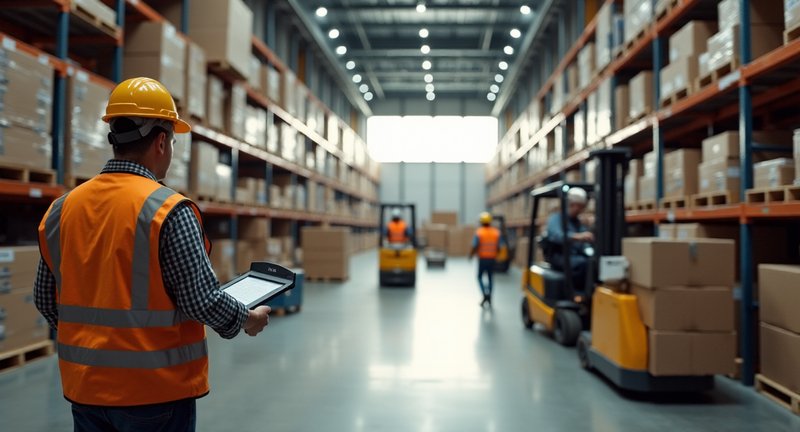
Over the years, I’ve found that optimizing this process comes down to communication and adaptability. The warehouse floor is always buzzing with activity, and it’s easy for things to go off track. But with clear instructions, good relationships with your team, and the right technology in place, you can navigate any challenges that come your way.
Freight management from warehouses may sound like a dry technical term, but it’s really where the action happens. If you’ve ever wondered what keeps businesses ticking, look no further than the daily hustle and bustle of a shipping operations from storage department. That’s where the gears of commerce truly grind.
The Essentials of Warehouse Shipping
Considering getting products out the door and into the hands of customers, there are a few key principles that make the process smooth and efficient. In my years working behind the scenes in logistics, I’ve come to appreciate the importance of these fundamentals both for cutting costs and keeping things running like a well-oiled machine.
One of the first things I always stress is streamlining inventory flow. This means everything from knowing exactly what’s in stock at any given time, to ensuring that the layout of the warehouse is optimized. Trust me, if your team has to zigzag across the entire warehouse just to find a single item, it’s going to cost you time and we all know time is money.
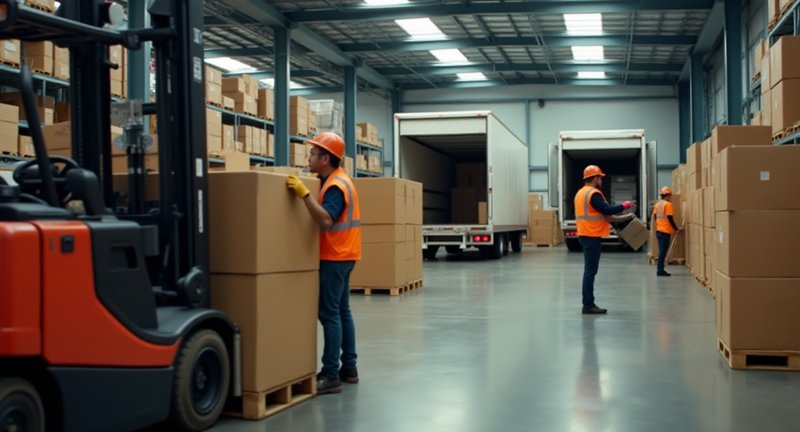
Next is handling and packing efficiency. You want to make sure that the packaging fits the product like a glove, not only to protect it during transit but to avoid wasting space. If boxes are packed with a ton of unnecessary cushioning, you’re paying extra for air! This brings us to another crucial point: maximizing transport capacity. Overstuffing a truck or leaving it half-empty? That’s a no-go. Every inch counts.
To summarize, here’s a quick breakdown:
- Optimize warehouse layout for quick access to goods
- Pack efficiently to protect items without wasting space
- Load vehicles to full capacity while avoiding damage
- Track inventory in real-time for accurate stock levels
- Always keep the customer experience in mind fast and reliable delivery makes a lasting impression
A smooth process isn’t just about what happens inside the four walls of the warehouse, it’s also about delivering a great experience on the other side. And that, at the end of the day, is what keeps customers coming back.
Understanding the Importance of a Robust Distribution Plan
When you’re building a successful business, especially in today’s fast-paced market, you can’t afford to leave your distribution plan as an afterthought. It’s the backbone of how your products reach customers, and believe me, I’ve seen plenty of businesses falter because they didn’t think it through. So, let’s unpack what makes a distribution strategy solid and why you should care about it more than just getting products from point A to point B.
First, a well-rounded distribution plan isn’t just about moving goods; it’s about timing, placement, and flexibility. You want your products to land exactly where your customers expect them, right when they need them. Here’s what I’ve found to be key elements:
-
Multiple Channels: Don’t rely on a single path. Think of retail, e-commerce, and direct-to-consumer options. Having alternatives ensures you’re not boxed in when unexpected disruptions happen.
-
Speed and Efficiency: Customers today expect fast delivery. Optimize your logistics network to minimize delays and keep the process lean. Believe me, the quicker the turnaround, the happier your customers.
-
Clear Communication: Keep everyone, from suppliers to delivery partners, in sync. When there’s transparency across the board, your whole operation runs smoother. No one likes surprises when they’re waiting on a shipment.
-
Scalability: As your business grows, your distribution needs to scale with it. Plan for the future so you’re not scrambling to meet demand later.
Neglecting any of these areas is a surefire way to end up with frustrated customers and strained resources. I’ve learned that taking the time to refine your distribution approach is one of the smartest moves you can make.
Key Components of an Effective Logistics Management System
When I think about effective logistics management systems, it’s like building the heart of an operation. You need every part working in harmony to ensure things flow seamlessly. Let me walk you through what I’ve found to be the essential components.
First, inventory control is a game-changer. It’s not just about counting stock; it’s about knowing where every item is, in real-time. Implementing automated tracking systems like RFID or barcoding can save you from countless headaches later on.
Second, transportation management deserves your attention. Coordinating routes, optimizing fuel use, and choosing the right carriers it all matters more than you might think. Using advanced algorithms to plan routes isn’t just for big companies; even small businesses benefit by cutting costs and delivering faster.
Now, there’s also demand forecasting. If you don’t anticipate what your customers want, you’re either going to overstock and waste resources or run out of popular products at the worst time. From my experience, investing in software that leverages historical data and predictive analytics can help keep you ahead of the curve.
Don’t forget supplier relationships. Partnering with reliable suppliers isn’t just about cost; it’s about trust. A solid relationship can mean the difference between a smooth operation and constant delays. Regular communication and shared technology systems go a long way here.
Also, a sometimes overlooked component is customer service integration. An efficient logistics system isn’t complete without ensuring the customer is part of the loop. Automated order updates, easy returns, and accurate delivery information build loyalty.
These are just a few of the gears that make logistics management tick. If you’re trying to scale up, you’ll need each one working flawlessly.
Streamlining Your Order Fulfillment Process for Maximum Efficiency
Streamlining your order fulfillment process is like perfecting a finely-tuned machine. It requires more than just sticking to standard routines; it’s about finding smarter, faster ways to get products to your customers with precision. I’ve learned from experience that efficiency is not just a goal but a necessity, especially when it comes to scaling your business.
Let’s start with a fundamental truth: delays in order fulfillment aren’t just frustrating they’re expensive. It’s crucial to smooth out the kinks in every step of your process to ensure maximum productivity. Here’s a practical breakdown of how you can improve:
-
Inventory Visibility: Knowing exactly where every item is located within your system is key. Investing in real-time tracking tools ensures that you can monitor stock levels and avoid delays from misplaced products or backorders.
-
Optimized Picking Routes: The shorter the time your team spends looking for items, the better. By organizing your product layout based on order frequency, you can reduce the walking distance and save valuable time.
-
Batch Processing: Grouping similar orders together allows your team to pick multiple items in one go. This method boosts efficiency, especially during high-demand periods when every minute counts.
-
Automation Tools: Automate what you can. From labeling to packing, leveraging technology to handle repetitive tasks frees up your workforce for more critical operations.
Streamlining isn’t a one-time task, it’s an ongoing process. Test, refine, and test again. Make sure to constantly review your methods and be open to innovations that can make things even smoother. Trust me, the rewards will be evident in your faster delivery times and happier customers.
How to Improve Your Packing and Labeling Procedures
I’ve seen firsthand how messy packing and labeling can derail even the smoothest of operations. One moment, you’re working efficiently, and the next, a mislabel has your entire system in chaos. I’ve learned it’s not just about getting things in boxes; it’s about doing it right.
Start by simplifying the process. Too many steps? You’ll get lost in the details. Fewer steps? Now, that’s where the magic happens. Streamlining doesn’t mean cutting corners; it means knowing exactly where the corners are and navigating them smoothly.
Labels need to do more than sit there looking pretty. They should speak volumes without saying a word. Invest in durable, easy-to-read labels. Trust me, there’s nothing worse than peeling stickers or faded print when you’re trying to meet a deadline.
Accuracy is king. Ever had a shipment returned because of a labeling error? You only need that to happen once to realize how critical this is. Double-check everything, even the smallest package. Your future self will thank you.
The right packing materials make all the difference. Cushioning, wrapping, securing it’s a dance that, if done properly, ensures that your products arrive in pristine condition. When I started paying attention to this, I cut damage rates in half.
But let’s not overlook technology. Digital tools can track everything from the moment an item is packed to the minute it arrives at its destination. If you haven’t explored these yet, it’s time to jump on board.
Choosing the Right Shipping Carriers for Your Business Needs
Choosing the right shipping carriers can make or break the flow of your business. Trust me, I’ve learned the hard way that not all carriers are created equal.
When picking a shipping partner, it’s not just about cost; reliability is king. A carrier that consistently delivers on time builds trust with your customers and saves you from logistical nightmares.
I also consider how well a carrier handles different types of goods. If you’re shipping fragile items or bulkier products, you need someone who knows how to treat them with care.
Don’t underestimate the importance of tracking technology, either. In today’s world, customers expect to know exactly where their orders are, and you want a carrier that offers real-time updates.
Customer service is another crucial factor. When things go wrong and they inevitably will you’ll want a carrier that can resolve issues quickly and without headaches.
It’s easy to get caught up in promises of low rates, but in my experience, paying a bit more for a premium service can save you more in the long run. The cheapest option often comes with hidden costs, like lost time or unhappy customers.
At the end of the day, it’s all about finding a carrier that fits your specific needs. Think about your products, your customers, and your priorities, then match that with what each carrier offers. Choose wisely, and your shipping process will run like a well-oiled machine.
Cost-Saving Tips for Reducing Freight Expenses
If there’s one thing I’ve learned, it’s that small tweaks can lead to big savings when it comes to freight expenses. The key is to dig into the details and make adjustments that others might overlook. You’d be surprised by how much money you can save just by optimizing packaging. By reducing the size of the boxes, you can fit more items on a pallet, which means fewer shipments overall.
Another tip? Don’t underestimate the power of negotiating with your carriers. Carriers are often willing to offer discounts if you establish a long-term partnership. If you ship consistently, they might even throw in extras like free delivery notifications or tracking, which can add up to significant savings over time.
Timing can also make a big difference. Avoid peak shipping periods whenever possible. Off-peak seasons and times allow you to access lower rates and faster service. You may need to plan ahead, but the cost benefits make it worthwhile.
Technology is your best friend here, too. By using freight management software, you can automate the comparison of rates across carriers and shipping methods. It’s like having a personal assistant that keeps your shipping costs in check while ensuring the most efficient delivery routes.
Also, consolidating shipments is a strategy that pays off. Instead of shipping multiple small orders, bundle them together. The savings on both time and transportation fees can be remarkable.
Enhancing Delivery Times Through Efficient Transportation Routes
Efficient transportation routes have been a game-changer for delivery timelines. I’ve seen firsthand how strategic route planning can shave hours, even days, off delivery schedules. It’s not just about speed; it’s about smart choices.
When mapping out routes, I always prioritize flexibility. The best routes aren’t always the fastest on paper, but the ones that account for variables like traffic, weather, and even road quality. You don’t want to rush straight into a bottleneck.
Another key aspect I focus on is minimizing stops. Every stop adds time, and more than once, I’ve found that by consolidating deliveries, we can cut down on unnecessary pauses. Think of it like reducing friction in a machine – fewer starts and stops mean smoother, quicker operations.
Technology has also played its part in my approach. With GPS and real-time tracking, I can now adjust routes on the fly. If there’s an unexpected obstacle, I can reroute in seconds, keeping the delivery on track without skipping a beat.
Of course, no matter how well you plan, there will always be surprises. That’s why I’ve learned the importance of building in a buffer – just enough cushion to absorb delays without sacrificing the overall schedule.
By focusing on these strategies, delivery times improve consistently. It’s not magic, just a mix of thoughtful planning and a willingness to adapt. And let’s be honest, faster deliveries keep everyone happier – from the logistics team to the customers waiting on the other end.
The Role of Technology in Enhancing Supply Chain Operations
The role of technology in enhancing supply chain operations is nothing short of transformative. Having worked in this space for years, I’ve seen how innovation drives both efficiency and adaptability, particularly in processes like Warehouse Shipping. It’s no longer just about moving boxes; it’s about precision, speed, and real-time insight.
When we talk about optimizing supply chains, a few key technologies stand out. Let’s break down the most impactful tools:
-
Automation: From robotic picking systems to automated conveyor belts, technology minimizes human error and accelerates order fulfillment. It can shave hours, sometimes even days, off the shipping process.
-
Internet of Things (IoT): IoT sensors allow you to track shipments as they move through the supply chain. Whether it’s monitoring temperature-sensitive goods or tracking a shipment’s exact location, this technology provides transparency and reliability.
-
Artificial Intelligence (AI) and Machine Learning: These tools analyze patterns in shipping data, forecasting demand and identifying bottlenecks before they become costly issues. When AI anticipates a delay, alternative solutions can be triggered instantly.
One experience I remember vividly was integrating a new warehouse management system with real-time tracking features. We went from days of uncertainty during Fulfillment center logistics to knowing where everything was, in real time. That peace of mind isn’t just valuable it’s priceless.
And let’s not forget the role of cloud technology. Cloud-based platforms allow for centralized control over multiple warehouses, streamlining operations, and ensuring consistency across regions. Plus, the ability to access information from any location can drastically reduce downtime.
In short, technology isn’t just enhancing supply chain operations it’s revolutionizing them. The results? Faster, smarter, and more reliable Dispatching from warehouses.
A Detailed Look at Warehouse Shipping
Let’s dive into the inner workings of getting goods from point A to point B. It’s a task that may seem straightforward, but once you’re in the thick of it, complexities start to emerge. From timing to coordination, every little detail requires precision.
I remember overseeing shipments that had to be aligned with seasonal demand spikes. The pressure to balance speed with accuracy is something you feel in your gut. A simple delay can ripple across an entire supply chain, throwing off timelines. But it’s not just about speed it’s about balancing efficiency with care.
I’ve learned that everything, from how pallets are stacked to the routes drivers take, has to be meticulously planned. It’s all about flow. And believe me, once the flow is broken, the domino effect is real. What seems like a minor misstep at the beginning can grow into a full-blown operational headache down the road.
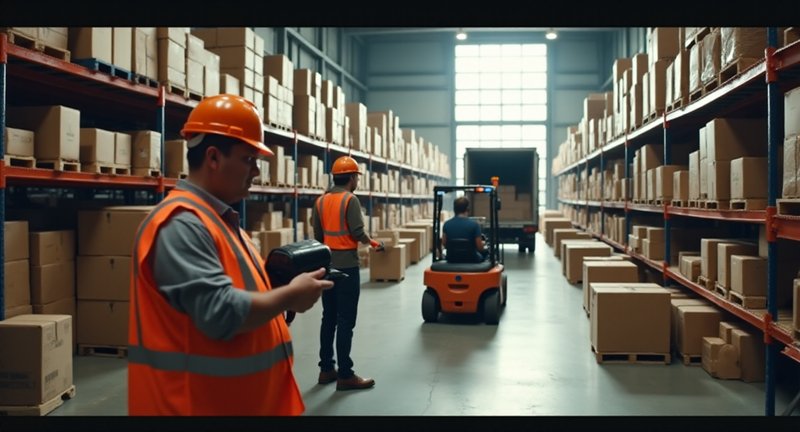
Then there’s the human factor. The best logistics software can only get you so far. It’s the people on the ground that make or break the process. Good communication between teams is key. When I worked on the floor, I would regularly check in with everyone to ensure no detail slipped through the cracks.
If I can leave you with one nugget of advice: it’s always the small things that matter most. Keep a keen eye on the details, and you’ll avoid the big disasters.
How to Automate Shipping Operations to Save Time and Money
Automation has revolutionized how shipping operations are handled. From my experience, once you start automating, you’ll wonder how you ever managed without it. Not only does it streamline processes, but it also saves an enormous amount of time and resources. Here’s a deeper look at how you can automate shipping and watch the savings roll in.
Key Benefits of Automation:
- Reduced manual errors: By automating shipping, you drastically minimize human error. No more wrong addresses or forgotten packages.
- Faster processing times: When orders come in, automated systems can instantly process them, calculate shipping rates, and even select the best carrier for the job all in a fraction of the time.
- Cost savings: Automation can integrate with your inventory and customer service tools to suggest the most cost-efficient shipping methods based on real-time data.
Steps to Automate Shipping Operations:
- Use shipping software: Invest in a platform that can automatically sync with your e-commerce site. This software can auto-generate shipping labels, track packages, and send notifications to customers.
- Integrate with your inventory system: Automation thrives when different parts of your business talk to each other. By connecting your inventory management system, you’ll know exactly what’s in stock and where it’s going.
- Leverage AI for route optimization: AI-powered tools can help identify the fastest, most cost-effective shipping routes, cutting down delivery times and fuel costs.
- Automated tracking and customer notifications: Keep your customers in the loop with real-time tracking updates. An automated system can notify them at each stage, reducing the need for manual intervention.
With shipping automation, you’re not just speeding things up. You’re empowering your business to scale, reduce stress, and improve the overall customer experience.
Best Practices for Managing Inventory and Reducing Shipping Errors
Managing inventory and minimizing shipping errors are like dancing a delicate waltz. From my experience, a few key practices can help you glide through this process with grace.
First, I found that maintaining a precise inventory system is crucial. It’s like keeping an organized toolbox when you know where everything is, finding the right tool becomes a breeze. Utilizing technology, such as inventory management software, can give you a real-time snapshot of your stock levels.
Next, communication is the heart of the operation. Imagine orchestrating a symphony; each instrument must be in tune to produce beautiful music. Regular check-ins with your team can ensure that everyone is on the same page regarding inventory status and shipping schedules.
Also, don’t underestimate the power of training. I’ve witnessed firsthand how a well-trained team can reduce errors significantly. When employees understand the process inside and out, they’re less likely to make mistakes that can lead to shipping mishaps.
As a matter of fact, consider adopting a quality control system. It’s like having a safety net during a high-wire act. Implementing checks at various points in the shipping process can catch errors before they reach the customer, saving you headaches down the road.
So, take these practices to heart, and you’ll find that managing inventory and reducing errors can transform from a daunting task into a smooth operation.
Leveraging Data Analytics to Optimize Shipping Costs and Performance
In my experience, one of the most powerful tools you can tap into to cut shipping expenses and boost overall performance is data analytics. It’s like having a compass that doesn’t just point north but gives you the entire map. When you start tracking the right metrics, you’ll quickly see opportunities to fine-tune your logistics operations and trim unnecessary costs.
Let me walk you through a few areas where data analytics makes all the difference:
-
Route Optimization: Analyze historical shipment data to identify patterns in delivery routes. Are there alternative routes that could save time or fuel? Optimizing routes isn’t just about getting there faster; it’s about ensuring that fuel consumption and labor costs are as efficient as possible.
-
Carrier Performance: Not all carriers are created equal. Use data to compare their on-time performance, costs, and even how well they handle fragile items. This insight can help you choose the most reliable carriers and negotiate better contracts.
-
Demand Forecasting: By studying customer behavior, you can predict spikes in orders, allowing you to adjust your shipping strategy accordingly. You’ll avoid the extra charges that come with rush deliveries or last-minute changes.
-
Inventory Levels: Data-driven insights can help balance your stock in a way that reduces unnecessary shipping between multiple distribution points. This means fewer trips, less fuel, and a leaner operation.
By focusing on these key areas, you can transform your shipping process from a necessary expense into a competitive advantage. Trust me, once you get into the habit of using data this way, you’ll wonder how you ever managed without it.
Choosing the Right Packaging Materials to Minimize Shipping Damage
I’ve spent years figuring out the right packaging materials to protect products during transit. It’s amazing how much thought goes into choosing the right stuff, and believe me, it’s not as simple as grabbing a box and tape. One overlooked detail, and you’ve got a disaster on your hands.
Think of packaging as your product’s first line of defense. A tough exterior might sound great, but it’s the interior cushioning that often saves the day. I once used a sturdy box but skipped padding. Result? A heap of broken goods. Lesson learned.
In relation to the choice of materials, I always look for versatility. Foam inserts, air pillows, and biodegradable peanuts each one has its own strength. Sometimes, the right material even depends on the weather. Too hot or too cold? It could mess with adhesives or cause cracking.
I always advise using customized solutions for fragile items. Generic packaging might save a few bucks, but tailored designs make sure the product stays snug. There’s nothing worse than hearing the rattle of a poorly packed item when you’re expecting perfection.
So, if you want to keep customers happy and products intact, start thinking about packaging like an investment, not just a formality. Trust me, it’s worth the effort.
Answers at a Glance
What is a warehouse in shipping?
A warehouse in shipping refers to a storage facility where goods are held before being transported to their final destination. It plays a critical role in supply chain management, acting as a hub for receiving, sorting, and dispatching goods. Warehouses often include inventory management systems to track stock levels and ensure efficient handling of orders. These facilities can range in size, depending on the scale of operations, and are equipped to store various types of products, from raw materials to finished goods, awaiting shipment.
What is a fulfillment shipping order?
A warehouse dispatch order is a document or electronic record that directs the warehouse to pick, pack, and ship specific items. It contains crucial information, such as the customer’s details, product codes, quantities, shipping methods, and destination. This order initiates the process of fulfilling a customer’s purchase by instructing warehouse staff to prepare the goods for delivery. The accuracy of a inventory shipment order is vital for ensuring timely and correct deliveries, minimizing errors, and maintaining customer satisfaction.
What is the shipping method in a warehouse?
The shipping method in a warehouse refers to the mode or means by which goods are transported from the warehouse to their final destination. Common shipping methods include ground, air, sea, or rail transportation. The choice of shipping method depends on factors such as the urgency of the delivery, distance, cost, and the nature of the goods being shipped (e.g., fragile, perishable, or hazardous materials). Warehouses often offer multiple shipping options to accommodate different needs, optimizing the process based on time and budget considerations.
What is US storage shipping?
US warehouse logistics shipping refers to the process of storing and dispatching goods from a warehouse located within the United States. It typically involves receiving items from suppliers, processing orders, and preparing goods for domestic or international shipment. This type of shipping is commonly used by businesses that sell products online or engage in large-scale distribution across the U.S. or globally. Utilizing US-based warehouses ensures faster delivery times for American customers and can also help streamline customs processes for international shipments.
What does shipping warehouse mean?
A shipping warehouse is a facility where products are stored before they are packed and dispatched to their final destination. It functions as a central point for managing inventory, processing orders, and coordinating shipments. Shipping warehouses are essential in the logistics chain, ensuring that products are organized, tracked, and shipped efficiently. These warehouses often employ advanced technology, such as automated picking systems and barcode scanners, to optimize workflow and maintain high accuracy in order fulfillment.
What is a warehouse delivery?
A warehouse delivery refers to the process of transporting goods from the warehouse to the specified delivery location, which could be a retailer, a business, or an individual customer. The delivery process involves preparing the items for shipment, selecting an appropriate transportation method, and ensuring the goods reach the destination in a timely and secure manner. Warehouse delivery is the final step in the order fulfillment process, and it often involves coordination with freight carriers, couriers, or shipping services to complete the transaction.
What is a freight warehouse?
A freight warehouse is a facility specifically designed for storing and managing goods that are to be transported by freight carriers, such as trucks, ships, or planes. These warehouses are equipped to handle large volumes of merchandise and may offer services like packaging, labeling, consolidation, and distribution of freight shipments. Freight warehouses are crucial for businesses involved in import and export operations, ensuring that goods are properly stored and prepared for bulk transportation across long distances, both domestically and internationally.
What does fulfillment shipping mean?
Warehouse dispatch refers to the process of moving goods from a warehouse to their final destination, whether it’s to customers, retailers, or distribution centers. It involves picking products from storage, packaging them appropriately, and selecting a shipping method to deliver them. Inventory shipment is a key part of the logistics process, as it ensures that products reach their recipients in good condition and within the expected time frame. Efficient storage shipping is critical for maintaining customer satisfaction and operational efficiency.
What is a warehouse receiving order?
A warehouse receiving order is a document or electronic record that instructs a warehouse to receive, inspect, and record incoming goods. It typically includes details about the shipment, such as the supplier’s name, item descriptions, quantities, and any specific handling instructions. The receiving order ensures that the warehouse properly logs the inventory upon arrival and verifies that the correct items were delivered. This document helps maintain accurate stock levels and is essential for inventory control and supply chain management.
What is the shipping process in a warehouse?
The shipping process in a warehouse includes several key steps: order receipt, picking, packing, labeling, and dispatching. First, the warehouse receives an order request, then the necessary items are picked from the storage areas. Next, the goods are securely packed, often with protective materials, and labeled with shipping information, including destination, tracking details, and any handling requirements. As a matter of fact, the packed goods are handed over to the chosen carrier for delivery. This process ensures orders are fulfilled accurately and efficiently.
What is the shipping method?
The shipping method refers to the mode of transportation used to move goods from one location to another. Common shipping methods include ground (trucks or trains), air, sea, or rail transport. The choice of shipping method depends on factors like the urgency of the delivery, cost, the distance between the warehouse and the destination, and the nature of the items being shipped. Businesses and customers can often choose between express or standard shipping, depending on their needs and budget.
What is the 3 method in shipping?
The ‘3 method’ in shipping generally refers to the three main categories of shipping: ground, air, and sea. Ground shipping involves transportation by truck or rail, usually used for domestic or short-distance deliveries. Air shipping is the fastest but often the most expensive method, ideal for urgent or international shipments. Sea shipping, while slower, is cost-effective for large, bulk shipments over long distances, commonly used for international trade. Each method has its advantages, depending on the delivery needs.
What is the shipping procedure?
The shipping procedure refers to the series of actions involved in preparing and sending goods to their final destination. It typically starts with receiving an order, followed by picking the required items from warehouse shelves, packing them securely, labeling with the correct shipping details, and selecting the transportation method. Once prepared, the items are dispatched to the carrier or shipping company. Throughout this procedure, accurate documentation and tracking are essential to ensure timely and safe delivery, while reducing the risk of errors.
Wow, this breakdown of shipping automation is spot on! We implemented shipping software a few years ago, and it was a total game changer. The manual errors from human oversight were a nightmare, especially when it came to missed shipments or wrong addresses. Automated tracking has been a lifesaver for our customer service team too customers love the real-time updates, and we spend way less time answering “where’s my order” queries. Plus, integrating with inventory systems makes everything run smoothly. I think anyone not leveraging AI for route optimization is really missing out. We cut delivery times and saved on fuel costs just by using it! All businesses should consider this if they haven’t already.
You nailed it when you mentioned the ‘domino effect’! I’ve seen a minor delay at the warehouse throw off an entire week’s deliveries. That gut feeling when you know something’s going wrong is all too real. Communication is definitely key! We’ve made it a habit to check in with drivers and packers daily to avoid any mishaps.
I couldn’t agree more about the impact of automation and AI in supply chain! I’ve seen firsthand how AI can predict bottlenecks and offer real-time solutions it’s a game changer! Once we implemented it in our warehouse, we saw improvements almost immediately. The peace of mind from real-time tracking is honestly priceless. Keep those innovations coming!
You’ve hit the nail on the head with route planning! Flexibility is key; I often find that avoiding traffic bottlenecks saves more time than just aiming for the fastest route. Minimizing stops is another smart strategy each stop really does add up. I love using GPS for real-time adjustments; it’s like having a secret weapon in logistics! Building in a buffer for delays is such a wise move, too. Overall, your thoughtful approach definitely leads to happier customers and a smoother operation. Keep up the great work!
Absolutely love the tips on tweaking freight expenses! It’s amazing how much you can save just by optimizing packaging. I started reducing box sizes last year and saw a significant drop in shipping costs. Negotiating with carriers is also underrated; building long-term relationships really does lead to discounts and perks. Your mention of avoiding peak times is a great reminder to plan ahead totally worth the effort for the savings!
I couldn’t agree more! Finding the right shipping carrier is like matchmaking for your business. I’ve had my share of logistical nightmares with unreliable carriers, and now I prioritize those who offer solid tracking options and great customer service. Trust is built on timely deliveries, and when my customers are happy, I’m happy! Plus, your point about handling different types of goods is spot on. It’s a game-changer when fragile items are treated with care. Investing in the right partner really pays off in the long run. Thanks for sharing these insights!
Wow, you hit the nail on the head about packing and labeling chaos! I once had a shipment returned because of a simple mislabeling error, and it taught me to value accuracy above all else. Simplifying the packing process while ensuring durable and clear labels has made a huge difference in my operations. I also appreciate your point about the right packing materials finding that balance between cushioning and efficiency really is an art. Technology has definitely transformed my packing process for the better. Thanks for sharing these valuable tips!
Your perspective on streamlining order fulfillment resonates so much with my experience in e-commerce! I’ve learned the hard way that even a slight delay can lead to customer dissatisfaction. Utilizing real-time tracking tools has been a game-changer for me as well, allowing for enhanced inventory visibility. I particularly love the idea of optimizing picking routes organizing items based on order frequency not only speeds up the process but also boosts team morale when they can complete tasks efficiently. Continuous improvement is key!
I completely agree that inventory control is the backbone of effective logistics management! Implementing automated tracking systems like RFID not only simplifies the process but also helps in maintaining accuracy, which is crucial. I once implemented a similar system, and it felt like a weight lifted off my shoulders. Plus, I could finally locate items in real-time, which saved me countless hours. Can’t wait to hear more about your insights!
You hit the nail on the head about distribution strategies! It’s so easy to overlook, but it really makes or breaks a business. I’ve seen companies thrive simply by diversifying their channels. It’s not just about speed; it’s also about having options when things go south. I also loved your point on clear communication it truly makes a difference. I think of it as the glue that holds everything together. A little planning goes a long way in avoiding those last-minute scrambles. Cheers to refining our distribution plans and setting our businesses up for success!
I love your focus on the key principles for streamlining logistics! It’s amazing how much smoother everything runs when inventory flow is organized. I once worked at a warehouse where the layout was a maze. We wasted so much time just navigating it! Once we reorganized for efficiency, we saw a massive increase in productivity. I can’t stress enough how important it is to pack smartly, too. I cringe every time I see unnecessary air in a shipment. Efficient packing not only saves money but also enhances customer satisfaction since the products arrive in perfect condition. And that breakdown at the end is spot on those points are crucial for any logistics operation! Let’s keep sharing tips on optimizing these processes; it benefits us all!
I completely agree with your take on warehouse shipping! It truly is like conducting a symphony, and every element has to be perfectly in tune for success. I remember my first large shipment, where I underestimated the sheer amount of coordination required. One missed deadline and suddenly everything felt chaotic! It’s fascinating how communication and tech play pivotal roles in ensuring smooth operations. I find that fostering good relationships with the team is equally important; everyone has to be on the same page. Those little nuances, like celebrating small victories on the warehouse floor, can significantly boost morale and productivity. Plus, with technology advancing, I’m excited to see how innovations will continue to refine our approach to distribution. Here’s to keeping the gears of commerce turning smoothly!